製造業の課題をローカル5GとAIで解決、愛媛県が挑む「地域シェア型スマート工場」:スマートファクトリー
製造業における少子高齢化による労働力不足、技能伝承に関する問題が顕在化している。特に地方での人材不足は深刻化しており、課題解決に向け試行錯誤が行われているところだ。その中でデジタル技術を活用した独自のアプローチで地域製造業の活性化に取り組んでいるのが愛媛県だ。愛媛県が進めた「ローカル5Gを活用した地域シェア型スマート工場」の実証実験について紹介する。
製造業において、少子高齢化による労働力不足は喫緊の課題だ。特に“匠”とされる高度な現場技術者の技術伝承問題は深刻さを増している。人材の数が限定される地方において人材不足感はより強まっており、産業を支えてきた地方自治体にとっても頭を悩ませる問題となっている。
こうした中で、先進デジタル技術の活用により、こうした課題の解決に取り組んでいるのが、愛媛県だ。数年前から総合的なDX(デジタルトランスフォーメーション)を推進する愛媛県は、地域産業のさらなる活性化を目指し「ローカル5Gを活用した地域シェア型スマート工場」プロジェクトを実施。ローカル5GやAI(人工知能)などの活用により、現場技術者の技能伝承の実現や、属人化の解消を推進する。同プロジェクトについて、愛媛県 産業技術研究所 所長の玉井浩二氏と、同プロジェクトに参画している富士通 Uvance本部 Sustainable Manufacturing People Enable事業部 シニアディレクター 野村進直氏に話を聞いた。
地域産業の活性化に向け、DXを担う人材や企業を育成
四国の北西部に位置し、風光明媚な景観や豊かな文化を色濃く残す愛媛県。夏目漱石の「坊っちゃん」や司馬遼太郎の「坂の上の雲」の舞台として知られているが、モノづくりにおいても存在感を発揮している。パルプや紙加工品の出荷額が全国1位(※)の「紙のまち」四国中央市や、今治ブランドとして全国に浸透した国内最大のタオル産地である今治市を擁するほか、化学、造船業など優れた技術力を持つ多種多様な産業が集積しており、独自性のある高品質な製品を生み出している。
(※)紙のまちランキング(紙関連の製造品出荷額等)16年連続日本一!
多くの製造業を抱える愛媛県において、現在大きな課題となっているのが、人材不足と技能伝承の問題である。「愛媛県内の中小製造業の多くが、熟練者の技術や技能を順調に継承できていない問題を抱えています。モノづくりを支えてきた熟練者が高齢化しており、本来ならば次の世代に技術や技能を伝えていく必要があります。ただ、人の採用が難しい状況や、属人化され過ぎていて伝承がうまくいっていないケースなど、人に関するさまざまな課題が山積しており、将来的な商品の生産性と品質の低下が懸念されています」と課題感について玉井氏は語る。
これらの課題解決を進めるカギとして、取り組むのが先進デジタル技術の活用だ。愛媛県では、数年前から県政全般にわたる総合的なDX推進体制を整備し、2021年にはさまざまな社会的課題の解決に向けたデジタル総合戦略を策定。同年にDX推進の司令塔となるデジタル戦略局を新設している。「最終的には育成した人材や企業を基盤に県内産業を活性化し、県外の企業を誘致する大きな目標があります。この長期的なビジョンの1つのステップとして、産業のDXを牽引(けんいん)するフラグシップモデルを作ることを目指しています」(玉井氏)。
この先進的なフラグシップモデルの創出を目指した取り組みの一環として新たに実施したのが、中小製造業のデジタル活用による課題解決を行う「ローカル5Gを活用した地域シェア型のスマート工場」プロジェクトである。
ローカル5Gを活用し作業の効率化と技能伝承を推進
「ローカル5Gを活用した地域シェア型のスマート工場」は、総務省が募集した「令和3年度課題解決型ローカル5G等の実現に向けた開発実証」に採択されたプロジェクトである。愛媛CATVを代表機関とした「愛媛県ローカル5G開発実証コンソーシアム」により実施した。コンソーシアムメンバーには、愛媛CATVや愛媛県、富士通の他、実証の場として金属加工業のツウテック、ユタカが参加している。
ポイントは、基地局設置などが高額となるローカル5Gを地域でシェアする仕組みにより、中小製造業でもローカル5Gを活用できる枠組みを作ったという点と、中小製造業のリアルな課題感に寄り添った現実的な課題解決にDXを活用したという点である。
2021年11月から2022年3月まで行った実証実験ではテーマとして「技術、技能伝承及び作業の効率化」を据えた。実証実験の場としてはコンソーシアムに参加しているツウテックと、ユタカにヒアリングを行い、製造現場でのリアルな困りごとにフォーカスし、実際に他の製造業でも展開できる典型的な課題解決への実証を進めることにした。ツウテックとユタカは、どちらも世界基準の精密加工技術を持つ中小製造業で、半導体製造装置や液晶装置、食品機械、医療機械、航空宇宙関連などさまざまな分野の金属部品加工を行っている。
ヒアリングの結果、今回の実証プロジェクトとしては「音響診断による設備の異常検知」「検品対象のAI画像解析」「スマートグラスを使った技術伝承、業務支援」の3つに取り組むことになった。玉井氏は「多くの中小製造業では、人員が不足しがちで熟練者が営業職など他の業務を兼任している場合も多くあります。熟練者が常に製造現場にいるとは限りません。そこで今回はこの製造現場の課題を解決するため、作業の負荷軽減と遠隔監視と遠隔支援、技能伝承などに貢献するソリューションを実証することにしました」と述べている。
音を使った異常検知で整備負荷を軽減
「音響診断による設備の異常検知」は、富士通が提供する「COLMINA(コルミナ)音響分析診断」を活用。熟練技術者が経験則によって行ってきた音や振動の違いによる設備の正常性の判断をAIによって行うものだ。
具体的には、金属の精密加工部品の加工で使うマシニングセンタに音響センサーを設置。センサーが収集した加工機器の作動音や稼働情報を、あらかじめ学習により破損推定モデルを構築した検知AIにより、正常か異常か判定する。異常を検知した場合には、アラートと工具情報、実際の音声データがローカル5Gを介して遠隔地の管理者に届く。管理者はその情報を参照し、必要があれば現場の作業者に部品交換を指示する。センサーデバイスは外付けのため、基本的にはどのNCマシンにも転用が可能だ。
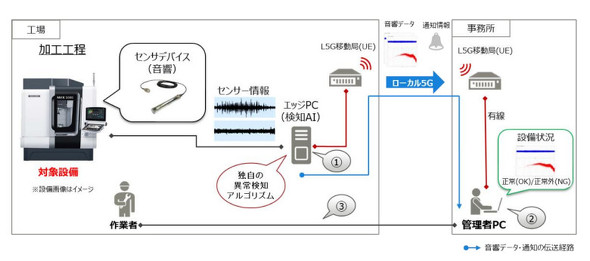
工具破損の検知システム構成イメージ[クリックで拡大] 出所:令和3年度 課題解決型ローカル5G等の実現に向けた開発実証 中小企業における地域共有型ローカル 5Gシステム による AI 異常検知等の実証 成果報告書
プロジェクトに参加し実際に導入を支援した富士通の野村氏は「マシニングセンタでドリルやエンドミルなどの工具は摩耗が進んだ状態になると作業品質が落ちたり、工具が折れたりする場合があります。熟練者は加工中の音によって摩耗の程度を判断しており、それによって工具が破損したり、作業の品質が落ちたりする前に交換する作業を行っていますが、熟練者が常に張り付いているわけにもいきません。この音の見極めの一部をAIで代替することで熟練者の作業負荷を軽減できます。ローカル5Gを活用することでリッチな音響データが活用できるようになりました。また、作業者のスキルに依存しない正常性の監視も可能となります」と語っている。
成果については、実証期間の短さや事前にアルゴリズム生成のための十分な音声サンプル数が確保できなかったという制約もあり、2社の工場での実証結果は、正常・異常の検出正解率は70%程度となったというが、野村氏は「異常をしっかり特定できるようになるには、データを取り溜めてAIに繰り返し学習させていくことが必要です。今回の実験で基本的な仕組みとして製造現場で運用し成果を生み出せる形は確認できました。ここで得た新たなデータを活用することで、より精度の高い検出ができます」と語っている。精度については今後さらに高めていく方向性だが、実際に成果としても不良品の発生率を20%程度削減でき、コストの削減に貢献できるめどは立ったとしている。
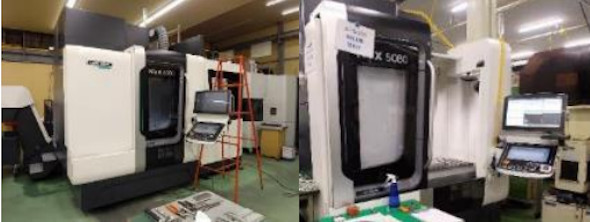
実際に実証を行ったツウテック(左)とユタカ(右)の機器[クリックで拡大] 出所:令和3年度 課題解決型ローカル5G等の実現に向けた開発実証 中小企業における地域共有型ローカル 5Gシステム による AI 異常検知等の実証 成果報告書
外観検査をAIで実施、人手が残る検査工程の負荷を軽減
「検品対象のAI画像解析」は、富士通が提供する「COLMINA 画像認識・異常検知AI」を活用し、熟練技術が必要とされる製品の検品作業をAIの高度画像解析で代用するものだ。富士通が独自で製作した外観検品装置を活用し、検品対象品を装置上に載せると6軸ロボットにより、さまざまな角度からワークを撮影。その画像基に事前に学習したAIで判定を行い、良品か不良品かを判断し振り分ける。不良品の判定が出た場合、遠隔地の管理者に画像が送られ、管理者による2次検査を行うという仕組みだ。
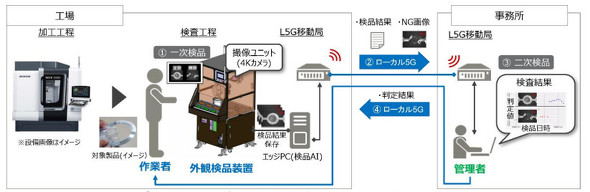
ロボットを活用した場合の外観検品の解析システムの構成図[クリックで拡大] 出所:令和3年度 課題解決型ローカル5G等の実現に向けた開発実証 中小企業における地域共有型ローカル 5Gシステム による AI 異常検知等の実証 成果報告書
基本的には外観検査は、全面的に人手で行う場合や一部を自動化している場合などがあるが、自動化している場合でも不良品を良品として通すわけにはいかないため、基準値を厳し目に設定している場合が大半だ。そのため実際には良品であっても不良品だとして、自動検査で引っ掛かる場合がある。これを2次検査で見極めて問題がなければ通常ラインに戻す作業を行うが、これらの作業負荷が非常に大きくなっている。そのため、AIを活用することで、この1次検査の精度を人の判断に近づけることで高めていくという点が目的の1つだ。もう1つは、1次検査でAIにより問題だと判断した箇所を明確に示し、2次検査の負荷を軽減するというものだ。
実証の結果、1次検査の良品に対する正解率は100%となり、これまで熟練作業者が確認していた時間(平均滞留時間)を30%削減することに成功したという。「『COLMINA 画像認識・異常検知AI』には、富士通が長年培ってきたAI技術とモノづくり現場での実践経験が詰まっており、専門的なスキル不要で高精度な画像認識アルゴリズムを自動生成できます。また、検品作業の際に非熟練者が判定に迷った場合には熟練者を呼んで判断を仰ぐケースもありますが、AIやロボットを導入した検査装置を導入することで、熟練者が遠隔地にいても検査状態をチェックできる環境を実現できます。そういう場所を問わない環境を構築するにはローカル5Gのような技術が有用です」と野村氏は利点について語っている。
スマートグラスで技能伝承を容易に
また、富士通は参加していないが、「スマートグラスを使った技術伝承・業務支援」についても実証を行っている。これは、非熟練者に対するスマートグラスを用いた技術指導や業務支援を遠隔地で熟練者やオペレーターが行う仕組みだ。非熟練者がスマートグラスを通して見た映像を遠隔地の熟練者に転送することで、リアルタイムで同じものを見ながら作業指導が実現できる。加えて、熟練者の作業手順をまとめたガイドラインや動画を、非熟練者がスマートグラスで見ながら作業することもできる。「実際に34%ほど指導時間の削減効果がありました。技術伝承や教育コストの削減は多くの製造現場にとっての課題となっていますが、これらを削減する効果があるということが分かりました」と玉井氏は手応えについて語っている。
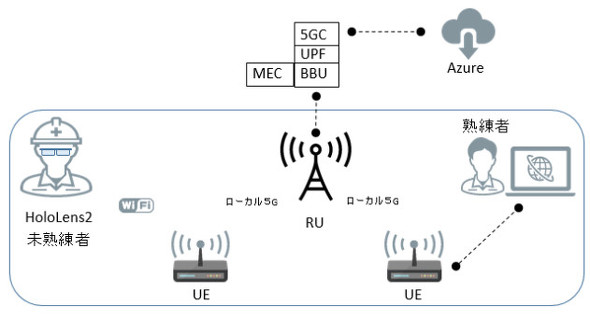
「スマートグラスを使った技術伝承・業務支援」のシステムイメージ図[クリックで拡大] 出所:令和3年度 課題解決型ローカル5G等の実現に向けた開発実証 中小企業における地域共有型ローカル 5Gシステム による AI 異常検知等の実証 成果報告書
実証実験で得たノウハウを横展開しモデルケースへ
今回の一連のプロジェクトについて玉井氏は「富士通さんを含め、多くの企業と愛媛県としてのビジョンを共有できた他、実際に活用できる仕組みを実証として進められたことは意義がありました」と手応えについて語る。今後は「今回のプロジェクトで得たノウハウを、県内の他の製造業や、他の産業でも横展開していきたいと考えています。スマート工場は、生産性や品質の向上だけではなく、今後の各社の働き方改革にも大きく貢献するものです。働きがいのある環境作りは確実に地域の活性化につながります。そのためにもモデルケースをここ愛媛県で成功させて、発信していきたいと考えています」と決意を述べている。
一方、富士通の野村氏は「地方の人材に関する問題の難しさを強く感じました。製造業の現場で人が関わる作業にDXをどんどん取り入れ、暗黙知だったものを形式知化し、最終的には人員の少ない中でうまく運用していく汎用的なモデルに昇華させたいです」と展望を語っている。
人手不足が強く叫ばれる日本経済の危機において、地方はその最前線に立たされている。ただ、逆に考えると、地方発で新たなモデルケースを作り出せれば、今後同様の苦境に立たされることが明らかな日本各地のあらゆる産業でも活用できる先進事例となり得る。そういう意味でもDXへのシフトを掲げ、県内産業のデジタル化やスマート化を支援する愛媛県の取り組みは、今後の国内産業での新たな方向性を示しているといえる。
Copyright © ITmedia, Inc. All Rights Reserved.
関連記事
- 画像AIで切粉トラブルを検知、工作機械メーカーが取り組む自動化と品質向上への道
- サステナブルでレジリエントな物流が、コロナ禍を支え社会課題を解決する
- 自動車メーカーも悩む“製造現場データの収集”、解決するために必要なもの
- 富士フイルムの最新鋭スマート工場、どうやって実現したのか
- 国内製造業のIoT活用はなぜ進まないのか、強さの源泉たる現場力を引き出せ
- 第4次産業革命を理解していない日本の製造業、データ活用で現場力を強化せよ
- ちょっと先の未来が見えるスマートモノづくり、CPSによる可視化で実現
- スマートファクトリーの前提となる「データの取り方」と「セキュリティ」
- CO2排出量17%、アラーム発生時間9割削減を実現、大和ハウスのIoT活用による「見せる化」
関連リンク
提供:富士通株式会社
アイティメディア営業企画/制作:MONOist 編集部/掲載内容有効期限:2022年7月14日