盤内機器の把握で古い設備の“ドカ停”を防げ ダイキン工業が取った対策とは:保全改革
製造現場の自動化によって設備が増え、保全業務の負担が高まっている。そのような中、「止まらない工場」を目指して保全が必要な設備の再点検を進め、効率化に取り組んでいるのがダイキン工業だ。ダイキン工業 堺製作所 臨海工場の保全業務変革を紹介する。
労働人口の減少に伴い、製造現場の自動化が進められている。ただ、自動化が進めば進むほど機械や設備が増え、さらにそのパフォーマンスが生産性や品質、生産量などに直接影響するようになっている。そのため保全業務の重要性はかつてないほど高まっているが、人手不足で保全人員を増やすのも難しい。従来とは異なるアプローチによる保全業務の効率化が求められている。こうした取り組みの第一歩として、工場内の各種設備を支える制御盤内機器の棚卸しを行い、一元管理で計画保全を実現しようとしているのがダイキン工業 堺製作所 臨海工場だ。
「止まらない工場」を掲げるダイキンの設備保全の取り組み
ダイキン工業は「空調事業」を中心とするグローバル企業だ。2022年度(2023年3月期)の売上高は3兆9816億円で、海外比率は約85%。グローバルで100以上の生産拠点を抱え、国内工場はマザー工場として新たなモノづくりの在り方を追求している。その一つである堺製作所 臨海工場は約9万500平方メートルの敷地に2つの工場を構える。1号工場はビル用マルチエアコンの室外機を年間約6万台生産し、2号工場は店舗オフィス用エアコンの室外機および空調機の心臓部となるコンプレッサー(空気圧縮機)を生産している。
堺製作所 臨海工場の1号工場は2018年に建て替えられ、最先端の機器や技術を導入した。2号工場は1990年の設立から30年以上が経過して設備の老朽化も進んでおり、十分な余裕を持って設備を保全することが難しくなっていた。大きな事故を起こさないように保全部門が細心の注意を払って既存設備を支えてきたが、例えば2017年度には板金ラインのプレス機の突発故障で2日間のライン停止を余儀なくされるなど、2号工場では設備の老朽化に起因する突発的な問題が避けられなくなりつつあった。
ダイキン工業 堺製作所 空調生産本部 臨海製造部 予防保全担当課長の酒井正起氏は「自動化された設備は止まっている時間が無駄になるため、できるだけ稼働時間を伸ばすことが重要です。さらに、自動化が進めば進むほど複数の工程を結んで工程間の無駄を省こうとしますが、そうなると1つの設備を止めることの影響が非常に大きくなります。抜本的に解決できるアプローチが必要だと感じていました」と語る。
ダイキン工業は1977年から独自のモノづくりの仕組みとしてPDS(Production of Daikin System)を展開して多品種混合生産などを実現。最近ではIoT(モノのインターネット)やAI(人工知能)などを活用してこれをさらに進化させている。
保全業務においても、「止まらない工場」を目指して「人材育成」と「設備診断技術開発」の2本柱で取り組んでいる。デジタル技術を活用した設備診断技術開発では、設備の膨大なデータから現在の状態を把握して故障診断を容易化するとともに、保全業務で扱うデータの一括管理によって保全工数の削減や業務効率化も可能にする。設備の常時監視環境を構築し、故障を予知することで設備を停止させることなくメンテナンスする予知保全への移行を目指している。
ダイキン工業 堺製作所 空調生産本部 生産技術部の宮下真司氏は「さまざまな設備の機種や機番などを、ワークにひも付くデータの形で収集しています。収集したデータはクラウド基盤に上げて分析し、その結果を保全チームにフィードバックして保全計画を進めています。全工場でこうした仕組みを実現することを目指しています」と説明する。
制御盤内機器を1つずつ確認する「制御盤点検サービス」
ここでハードルになったのが「古い設備」だ。1号工場はリニューアル時にIoTを含めた予知保全の仕組みを導入した。だが2号工場は古い設備が多く、改善活動の中で順次入れ替えており統合的な管理が難しくなっていた。そのため、設備やその中で使われている機器の現状を把握するだけでも非常に大きな手間が必要だった。
そこでダイキン工業が相談したのがオムロン フィールドエンジニアリング(OFE)だ。OFEはオムロングループのエンジニアリング企業で、もともとPLC(Programmable Logic Controller)のリプレースサービスなどの取引関係があった。こうして、OFEが試験的に展開している「制御盤点検サービス」を実施することになった。
「2号工場で、制御盤内のマグネットスイッチの交換ができていないという相談を受け、制御盤点検サービスが役に立つと感じました。制御盤点検サービス自体は以前にダイキン工業さまの別の物流倉庫で実施していたため、まずは2号工場でも進めてみようという話になりました」とOFE IB事業本部 IB営業部 IB営業三課 課長代理の加藤尚氏は語る。
制御盤点検サービスは、制御盤内の機器や配線を1つずつ確認し、PLCをはじめとする各種機器の状態や保守状況などを確認するサービスだ。交換が必要であれば交換した上でレポートを作るため、今後の計画保全用の台帳作成にも利用できる。これらは簡単そうに見えるが実は非常に大変な作業を伴う。特に2号工場は設備も制御盤内の機器も非常に多い。機械の間などが非常に狭い場合もあり、物理的に作業しにくいという難しさもある。
作業に携わったOFE IB事業本部 IB西日本エンジニアリング部 IB西部SE課の藤本太平氏は「工場内の制御盤や部品点数、種類の多さに驚きました。1つの制御盤で100台分のマグネットスイッチを交換するケースもあり、こうした作業を日々さまざまな保全作業に追われている現場の保全担当者だけで行うのは難しいと実感しました」と振り返る。
誰がやっても大変な作業ではあるが、OFEがこうした作業を効率的に行えるのは「制御機器の知見」と「制御盤のノウハウ」があるためだ。藤本氏は「オムロングループとしてPLCのリプレースについての知見があります。PLCのプログラムやネットワーク設定などのデータをバックアップしたり、部品交換に関しても配線のチェックリストなど過去の実績の中で用意したツールや手法などを活用できたりするなど、難しい作業も短時間で行えます」と説明する。
制御盤点検サービスで得られたレポート結果を設備部品情報の管理に特化したオムロンのクラウドサービス「保全Navi(※)」に登録して管理することで、計画保全のベースとなる「使用機器の見える化」が実現する。ダイキン工業も制御盤点検サービスで得られた情報を保全Naviに登録しており、これをベースにリプレースの計画などを立案し、「事後保全」から「予防保全」に切り替える重要な基盤を作れたという。
OFEと二人三脚で取り組んだダイキン工業 堺製作所 空調生産本部 臨海製造部 予防保全担当の藤谷宣典氏は「古い設備の現状把握は工場側でも必要だと感じてはいましたが、発生する工数の多さ故になかなか手を出せなかった領域です。それを代替してもらえたことは非常にありがたいと感じました。全ての制御盤を開けて機器の棚卸しをしてもらえたことで各種対応を円滑に行う土台ができたと考えています。突発停止の真因把握などにも貢献するとみており、さらに機器更新の計画立案にも役立つなど、総合的に考えると大きなメリットが生まれています」と語る。
(※)保全Naviは、生産設備を有する国内ユーザー向けにオムロンが提供するクラウド有償サービス。ユーザーが設備単位で使われている制御機器を登録することで、使用中機器の生産終了情報など保全リスク情報の見える化ができる
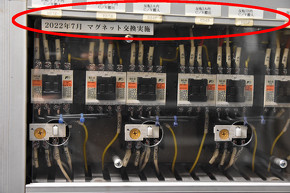
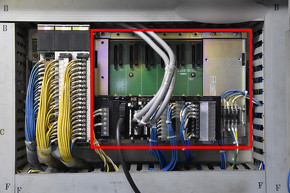
さらなるドカ停削減へ データの積極的な活用も
今後、ダイキン工業は「止まらない工場」を実現するため、さらなるドカ停防止に取り組む方針だ。ダイキン工業の酒井氏は「自動化によって保全業務の重要性が高まる中で、今回の取り組みはまだまだ第一歩とも言うべきものだと考えています。減ったとはいえまだ設備の故障はあり、それをゼロに近づける施策を打っていきます。ただ、そこに無尽蔵にリソースを割くことはできないため、優先順位を付けて進めるつもりです。影響が大きくて常時監視が必要なところはIoTやAIなどのデジタル技術も積極的に活用していきます。そうした対応が難しいところは、OFEさんのサービスなども利用してできる限り効率的に計画保全が行えるようにします」と展望を語る。
OFEの加藤氏は「今回の成果を生かして、今後はダイキン工業さまの他の製作所にもサービスを広げていきたいと考えています。また、効率的な仕組みや最適なサービスを模索します」と語る。さらに、新たな付加価値としてデータの活用を検討している。「点検してリプレースするだけでは新たな価値を生むことはできません。製造現場内でのデータ活用が浸透する中で、スマートファクトリー化の一歩として制御盤内機器でのデータ収集や活用ができる仕組みづくりのため、PLCのリプレース時に最新のネットワークユニットを追加するなどの提案も実施していきます」と加藤氏は今後の方向性を説明する。
自動化が進み、設備起因の突発停止リスクが上がる中、限られた人員や予算による保全の高度化や効率化に悩む製造現場は多い。日々の業務に追われて事後保全に終始し、古い設備で使われている機器の棚卸しもままならないことも多い。そのような場合は、制御盤を知り尽くし、制御盤を一つずつ開けて点検するような労力も惜しまず対応してくれるOFEや保全に関する各種商品や人材育成を含めたサービスを提供するオムロンに相談してみるのも手だと言えるだろう。
Copyright © ITmedia, Inc. All Rights Reserved.
関連記事
- 人の“多様性”をデジタルで力に、オムロン京都太陽のモノづくり革新
- 作業時間ばらつきを28%低減、スマート工場を実現する“超現実的”サービスの真価
- 顧客の現場力も高め、課題解決まで付き合い続けるオムロンFAサービスの実力
- 工場設備で23%の省エネを実現、真空装置メーカーが取り組んだIoTの現実的価値
- リフトに自分で乗ってスーツを運ぶ搬送ロボ、紳士服メーカーが目指す一歩先の自動化
- アイシン・エィ・ダブリュが目指す理想像、“人が活躍”のスマート工場とは
- オムロンとFUJIが取り組む“面の自動化”、モバイルロボットと実装機が連携する意味
- 搬送自動化のカギを握るモバイルロボット、オムロンが考える普及の5つのポイント
関連リンク
提供:オムロン株式会社、オムロン フィールドエンジニアリング株式会社
アイティメディア営業企画/制作:MONOist 編集部/掲載内容有効期限:2023年12月28日