マツダのからくりを通じた人づくり、工場は創意工夫と成長の場:からくり改善(3/3 ページ)
工場では多品種化と生産性向上の両立が求められており、そこでは人がより効率よく安全に作業するための工夫も欠かせない。マツダは長年からくりを活用した作業改善に力を入れてきた。同社がからくりを用いた改善に取り組む理由を聞くとともに、「からくり改善(※)くふう展2018」(主催:日本プラントメンテナンス協会)に出品された同社の作品の一部を紹介する。
12本のボルトを一気に仮締め
従来は手作業で行っていたトランスミッション組み立てにおけるボルトの仮締め作業を一気に行えるようにしたのが、「マッハ締付けジョーズ」だ。トランスミッションを製造している防府工場中関地区の作品になる。
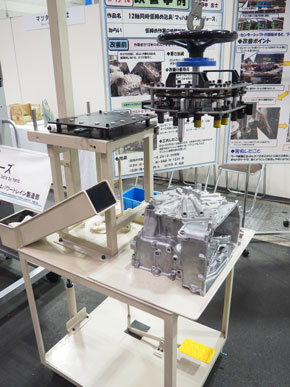
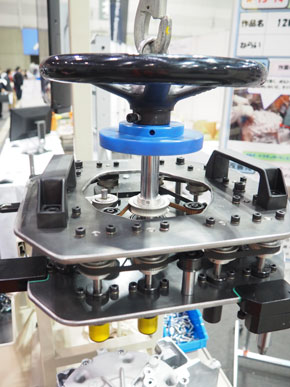
トランスミッションのエンドカバーの取り付けでは、ねじ穴が浅くボルトが倒れるため仮締めが必要になる。従来、作業の早い若手でも12本のボルトの仮締めには30秒かかっていたという。これをベルトとプーリーを利用したからくりによって、10秒以内で仮締めできるようにした。
まずスロープを流れてきたボルトがプレートの12の穴に自動ではまる。続いて上から吊り下げたマグネットの入ったソケットをボルトに密着させる。このソケットをガイドピンに沿って下ろし、上部のハンドルを回せば一気に仮締めが完了する。また作業に掛かる力も非常に軽い。
仮締めをする際は、ボルトを回すためのベルトがセンタープーリーを介して動き、12軸を一斉に回転させる。ボルト穴が不均一な配置のため、調整可能なテンション機構を1つ、ベアリングを入れたテンション機構を5つ配置したという。
誰でもシェルパレットを運搬
鋳型のパレットの運搬をレバーの開閉だけでできるようにした装置が、本社工場から出展された「楽々まえちゃん」だ。この装置は女性を含むメンバーが開発、解説も女性が行っていた。
砂型を載せるためのパレットは1枚15kgで、男性でも重く大変さが伴う作業だった。一方パレットに乗せる砂型の重量は340kgとなる。そこでパレットの取り出しと移動を、重力と元からある動力を使用して、レバーの切り替えだけでできるようにした。
積み重ねられたパレットは、4つのらせんねじによって1枚ずつ切り出され、搬送レーンに送られる。レーンは5度の傾斜があり、傾斜の先にあるチェーンについているストッパーを押し下げると、チェーンの動きの向きがかさ歯車によって変換され、スクリューの動力になるという仕組みだ。
「鋳物の現場なので、らせんねじは自分たちで制作した」という。まず3D CADで、パレットを1枚だけ取り出せる幅などを検討してモデリングし、3Dプリンタで出力して確認した後、実物を作成したということだ。これにより「女性や高齢者でも作業ができるようになった」と話す。
Copyright © ITmedia, Inc. All Rights Reserved.
関連記事
製造業をカイゼンできるのはIoTだけじゃない、“からくり”がもたらす安全と効率
ロボットを導入するのは難しいが、手作業では効率化や安全性に課題がある……生産ラインのそんな困りごとを解決するのが「からくり」だ。動力に頼らず、ワークの自重やシンプルな動きを利用することで、安全に効率を高められる。知恵と発想がつまったからくりの数々を紹介する。「からくり改善」で躍進、重力と知恵で実現する自動化で年率30%成長
工場の自動化ニーズが高まる中、安価で作業負荷を軽減できる“からくり”への関心が高まっている。その“からくり”を支援して年率30%成長を見せているのがアルミフレームを提供するSUSである。同社の“からくり”の提案を取材した【訂正あり】。製造業をカイゼンできるのはIoTだけじゃない、“からくり”がもたらす安全と効率
ロボットを導入するのは難しいが、手作業では効率化や安全性に課題がある……生産ラインのそんな困りごとを解決するのが「からくり」だ。動力に頼らず、ワークの自重やシンプルな動きを利用することで、安全に効率を高められる。知恵と発想がつまったからくりの数々を紹介する。スマート工場を支える“現場力”に再注目が集まった2017年
2017年に公開したMONOist FAフォーラムの記事をランキング形式で振り返る。公開記事の1年間分のデータを集計した上位記事とそこから見えるFA業界の状況について紹介する。2016年に続き、トップ10のほとんどがIoTなどスマート工場に関する話題となったが、工場での実導入の成果についての記事が増えていることが特徴だ。マツダの「モノづくり革新」を推し進めるTPM活動の神髄とは
本連載「いまさら聞けないTPM」では、TPM(Total Productive Maintenance)とは何か、そして実際に成果を得るためにどういうことに取り組めばいいかという点を解説する。最終回の第7回は、TPM活動の実践事例として、2015年3月末までマツダの常務執行役員を務め、「モノづくり革新」の推進に貢献した中野雅文氏の寄稿をお届けする。