大河原デザインのトミカ、3Dプリンタ試作と本格量産の“溝”を埋める:DMS2016
ストラタシス・ジャパンは、「第27回 設計・製造ソリューション展(DMS2016)」において、全日本製造業活性化計画(JMRP)とメカニックデザイナーの大河原邦男氏、タカラトミーなどと連携して開発したトミカ「イグザインBARID」を展示した。
ストラタシス・ジャパンは、「第27回 設計・製造ソリューション展(DMS2016)」(2016年6月22〜24日、東京ビッグサイト)において、全日本製造業活性化計画(JMRP)とメカニックデザイナーの大河原邦男氏、タカラトミーなどと連携して開発したトミカ「イグザインBARID」を展示した。
イグザインBARIDは、大河原氏がJMRPに提供したオリジナルロボット「イグザイン」のデザイン要素をJMRP側でクルマに落とし込んだもの。大河原氏が監修を行っている。今回の展示は、イグザインBARIDのデザインを使ったトミカの短納期/小ロットによる試作量産を目的とする「クロスエンジニアリングプロジェクト」の成果になる。
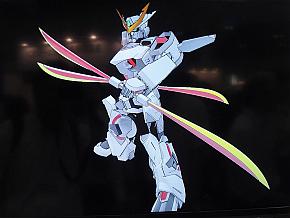
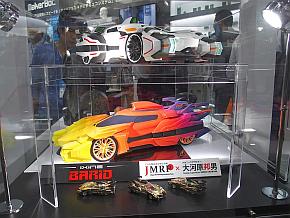
同プロジェクトでは、イグザインBARIDのトミカを構成する各部品の設計をタカラトミーが、「デジタルモールド」と呼ばれる3Dプリンタを活用した樹脂金型による部品の生産をストラタシス・ジャパン、スワニー、キャステム、中辻金型工業が担当した。
一般的なトミカの場合部品点数は12個だが、イグザインBARIDは約2倍の22個の部品で構成されている。ボディーやシャシーをはじめ22個の部品のデザインの出来栄えや、組み立てしやすい部品の勘合などさまざまな条件を合わせこみながら、最終的に100台のイグザインBARIDのトミカを組み立てた。イグザインBARIDの外観デザインがある状態から、100台のイグザインBARIDのトミカを組み立て終わるまでの期間は3週間と極めて短い。
試作用途で3Dプリンタの利用が広がっているものの、数十〜数百といった小ロット量産には適しているとは言い難い。また、3Dプリンタで積層造形した製品と、金型を使って量産した製品では質感なども異なってくる。何より、3Dプリンタでの試作に用いた設計データは、量産の製造設計にそのまま適用できるわけではない。今回のプロジェクトは、3Dプリンタによる試作と、金型による量産の間にある溝を埋める取り組みになっていると言っていいだろう。
なお、最後の組み立て工程は、商店街の空きスペースを利用した内職ワークスペース(長野県伊那市)で行った。“内職”として組み立てを行ったのは、引退後の60〜70歳の高齢者や主婦である。
JMRPでは今後もイグザインを使ったプロジェクトを進めて行く予定。ドバイでのイグザインBARIDの実車作成や、クラウドファンディングによるイグザインのパワードスーツ化などだ。
Copyright © ITmedia, Inc. All Rights Reserved.
関連記事
設計・金型・成形のエキスパートたちが実現した“ランナーレス”なプラモデル
バンダイは「東京おもちゃショー2015」(会期:2015年6月18〜21日、場所:東京ビッグサイト)に出展し、同年9月に販売開始を予定する新型プラモデル「超次元変形フレームロボ」の試作モデルを初公開した。オリジナル「ミニ四駆」ボディを手に入れよう!
タミヤの「ミニ四駆」を題材に、無償3次元CADでミニ四駆の“オリジナルボディ”を3Dモデリングし、3Dプリンタで出力するまでを解説する連載。第1回では、ミニ四駆のレギュレーションやシャーシの種類、実際に3Dモデリングを進める前に押さえておくべきポイントについて解説する。CAD経験ゼロのミニ四駆レーサーが、ミニ四駆“3Dモデラー”になるまで
「3Dモデラボ カーデザイン コンテスト 2016」の開催を記念し、「Autodesk Fusion 360」を活用してオリジナル「ミニ四駆」ボディーを製作する圓田歩さんと、Fusion 360のエバンジェリストである藤村祐爾さんの対談をお届けする。ガンプラは1つ屋根の下で作られる
ガンダムのプラモデル(ガンプラ)の設計・製造の世界は、家電や産業機械とは随分と違う設計思想やカルチャーを持つ。ユニークなテーマでいつもと視点を変えることにより、モノづくりのヒラメキが得られるかも!?(編集部)