豊富なエンジニア体制と「ハミダス」精神、ニチレイフーズの進化の秘訣とは:ものづくりDXのプロが聞く(1/3 ページ)
Koto Online編集長の田口紀成氏が、製造業DXの最前線を各企業にインタビューする「ものづくりDXのプロが聞く」。今回は、ニチレイフーズのエンジニア組織や開発体制、スマートファクトリー構想などについて伺いました。
本連載は製造業のDXに携わる人のためのメディア「Koto Online」に掲載された記事を、一部編集した上で転載しています。記事の情報は、2024年2月時点のものです。Koto Onlineは業界のトップランナーへのインタビュー等を通し、製造業の未来に触れられるコンテンツを発信しています。
実際に炒めた冷凍チャーハンや、冷凍の冷やし中華など、私たちの生活に身近な冷凍食品や加工食品の世界で数々の革新的な商品を生み出してきた、ニチレイフーズ。スマートファクトリーの実現に向けて、さらなる進化を目指しています。
「ものづくりDXのプロが聞く」は、コアコンセプト・テクノロジー(CCT)CTOでKoto Online編集長の田口紀成氏が、製造業DXの最前線を各企業にインタビューするシリーズです。今回は、ニチレイフーズのエンジニア組織や開発体制、スマートファクトリー構想などについて、同社の生産統括部技術戦略部・装置開発グループリーダーの塚本真也氏にお話を伺いました。
食品メーカーとして異例のエンジニア体制、装置も自前で開発
田口氏(以下、敬称略) ニチレイフーズ様は読者の皆さまにも大変なじみが深いと思いますが、改めて、御社の事業内容について教えてください。
塚本氏(以下、敬称略) 旧帝国水産統制が再出発して1945年に設立された、日本冷蔵が前身となります。1985年に片仮名のニチレイとなり、2005年の分社化を経て、現在、ニチレイフーズとして加工食品事業を行っています。
主に取り扱っているのは米飯類やチキンをはじめとした冷凍食品や、カレーなどのレトルト食品を生産しています。皆さんに目にしていただくことが多いのは、スーパーで販売している家庭用の冷凍食品などですね。その他にも、コンビニエンスストア様や学校給食などで活用いただく業務用商品も手掛けています。
北海道から九州まで、全国に15の自営工場があり、2023年4月に稼働を始めた福岡県宗像市にあるキューレイ第3工場が、現在一番新しい工場です。
田口 塚本様のご経歴についても、お聞かせいただけますか。
塚本 私は2002年の入社以来、一貫してエンジニアリング畑で仕事をしてきました。入社後すぐに食品工場に配属され工場の業務改善に携わったり、当時のグループ会社に出向し、24時間365日稼働する特殊な工場で通常と異なる作り方を学んだりしました。
最初に工場に配属されるのは、まず現場のものづくりを学ぶという当社の特徴でもありますね。また、海外に新会社を設立して工場を作るプロジェクトに参画し、ゼロから立ち上げる経験なども積んできました。
技術戦略部に配属後、担当していたのは、品質保証に関わる分野の技術開発です。例えば工場では、最後の工程としてX線検査や金属検査などを行います。
当時は製品を流して通過すればOKという作りで、検査を通ったものはそのまま流していたのですが、検査した製品全てのデータを取得して一つ一つひも付けしていく方式に変更したんです。冷凍食品のパッケージを見ていただくと、賞味期限の下に時間が書いてありますが、それは製造時間が全て記載されているんですね。
今ではそれがスタンダードになっていますが、20年ほど前はまだそうした機能がある検査機器はありませんでした。そのため、検査機器のメーカーさんと「塚本さん、NGデータだけでなく、全部のデータを取るんですか?」なんて言われながらやりとりして、全てのデータを集約できるシステムを作り上げていきました。DXの走りみたいな取り組みですね。
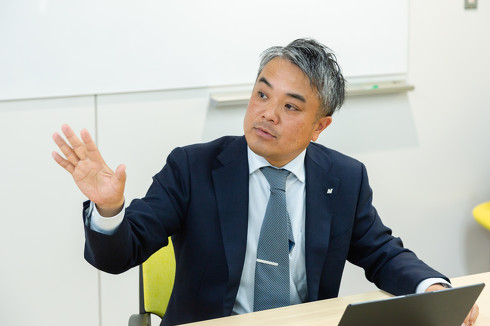
「検査機器のメーカーさんと『塚本さん、NGデータだけでなく、全部のデータを取るんですか?』なんて言われながらやりとりして、全てのデータを集約できるシステムを作り上げていきました」(ニチレイフーズ 塚本氏)[クリックで拡大]出所:Koto Online
田口 御社のエンジニア組織としては、どのような体制になっているのでしょうか。
塚本 ほかの食品メーカーさんと比べると、当社のエンジニア組織は多くの部隊があります。私が所属している、例えばチャーハンを炒める新しい機械などを開発する装置開発グループや、システムの内製などDXやAI活用を担当する生産革新グループなどは特徴的なグループです。
食品メーカーの場合、生産工場にある技術グループや本社のエンジニアグループがあり、そこで工場や生産ラインといった設計全般を担当するのが一般的です。装置開発やDX推進のエンジニアグループが個別にあるのは、珍しいのではないでしょうか。
田口 装置やシステムというのは、どのぐらいまで内製しているのでしょうか。
塚本 プログラムを作るところに関しては自分たちでやっています。設計も詳細のところは外部にお任せしますが、イメージなどは内部で作っていますね。今後はCADなども自社で取り組もうとしていて、今までよりもさらに自分たちで、という方向で進んでいますね。
全て外部のシステム会社にお願いしていた時期も過去にはあったのですが、なかなかうまくいかなかったんです。仕様を伝えるのが難しいですし、出てきたものが全然違ったり、使い始めると不具合があったりして、何度も直してもらうことで余計なお金も時間もかかってしまいます。その経験から、2005年ごろから自分たちでやっていこうという方向に舵を切りました。
田口 そんなに以前から自社で取り組んでいるというのは驚きですね。伺った体制についても、確かに一般的な食品メーカーさんのエンジニア組織とは層の厚さの違いを感じます。それだけ時間をかけて構築してきたものがあるんですね。
塚本 他社さんからお声がけをいただいて情報共有する機会もあるのですが、「どんなふうに自社でやっているのですか」と聞かれてお話すると、やはり驚かれることが多いですね。
20年ぐらい前から取り組んで人材教育もしていて、「プログラマーが各工場にいます」とお伝えすると、全然違いますとよく言われます。いわゆるエンジニアリング会社が自社の中に1つあるようなもので、ここは当社のメリット、強みだなと感じます。
CORE CONCEPT TECHNOLOGIES INC.