OKIのフラグシップスマート工場が始動、「外部化」見据えた実践の場として活用:スマート工場最前線(3/4 ページ)
OKIは、本庄地区(埼玉県本庄市)の新工場「OKI本庄工場H1棟」の本格稼働を開始し、自動化を実現する新設備などを公開した。
外観検査装置や協働ロボットなど人の作業負荷を軽減
自動化領域の拡大に加え、人の作業を支援し作業負荷の軽減を行うさまざまな仕組みも導入している。組み立て作業では、協働ロボットを使用し、作業者とロボットが協力して組み立て作業および検査作業を行う工程なども用意。作業者はロボットでは対応が難しい複雑な作業を担い、ロボットは動作は単純だが精度が必要な作業を行う。全ての作業を自動化するのではなく、人と機械の強みを組み合わせた形で生産性を高めている。
組み立て工程内でのさまざまな作業のミスを防ぐために外観検査を自動で行う検査システムも用意している。作業ミスや不具合の早期発見を行う。例えば、製品に貼付するシールの印字をカメラで撮影して検査を行い、印字ミスが起こらないように常に確認できるようにしている他、組み立て作業のネジ締めのミスがないかをカメラで撮影して確認。工程内で作業ミスの把握が行えるようにした他、トレーサビリティーの確保にも貢献する。
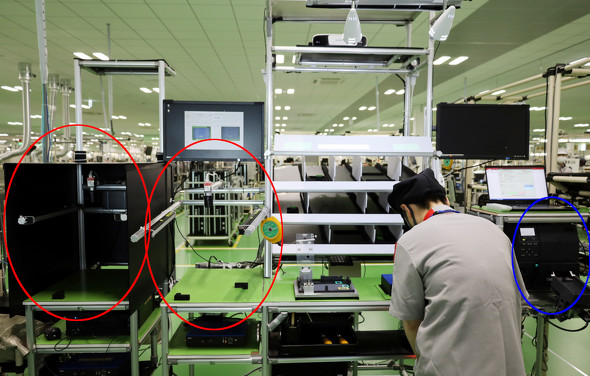
組み立て工程内に組み込まれた外観検査システム。赤丸部でネジ締めや完成品の検査を行っている。ワークを設置するだけで簡単に確認ができる。青丸部はラベルプリンタのラベル内容の検査を画像で行っている[クリックで拡大]
さらに、これらを組み合わせた理想の製造ラインとして「DXモデルライン」なども稼働させている。こちらはホームネットワーク用のルーターの製造工程で導入され、ライン生産であるはんだ付け工程と、セル生産である装置生産工程を連結し、同期させることでモノの滞留の少ない生産ライン構築を実現している。
このラインでは、まず各工程のデータ収集と蓄積を行い、各工程での作業履歴をサーバに記録している。これらの作業記録と組み合わせて検査工程での検査結果を自動収集している。また作業状況は工程内に設置されたカメラで映像としても記録している。これらを照らし合わせることで製品1台を作り上げるサイクルタイムが自動で出せるようにしている。さらに、工程内で問題が起きた場合でもデータを基に発生箇所に立ち返ることができ、すぐに問題の要因を突き止めて対処できるようにしている。これらの情報を蓄積していくことで、データ分析を基に、作業方法や治工具、設備、人員配置の最適化などを進められるようにしていく計画だ。
自社開発の自動倉庫システムも
自社開発の自動倉庫システムも新たに開発した。電子機器の製造工程では、基板への部品実装を行うため、多くの部品がテープ状のリールで納品されている。ただ、数多くの種類の部品を扱うために、これらのリールの管理や、個々のリール内に収められている部品の数の管理などに多くの負荷がかかっていた。
例えば、リール内の部品は実装で使用した残りなどを従来は人手でテープを回転させる装置にかけて計測していた。また、部品を種類ごとに棚で管理していたが、作る製品が増えれば増えるほど、棚の数が大幅に増えておりスペース効率の点でも問題があった。そこで、まずリール内の部品の数を正確に素早く計測できるようにX線カウンタを導入し、従来は計測に3分くらいかかっていたのを約10秒で行えるようにした。加えて、リール棚のフリーロケーションを実現。リールのバーコードおよび、棚の各場所のアドレスバーコードをスキャンしてひも付けて管理することで、空いている場所に部材をすぐに収納しても場所を把握できるようにした。これにより、保管場所の無駄を約20%削減できたという。リール棚にはLEDライトが付いており、部品をピッキングする際は、必要な棚のLEDが点灯することで、迅速なピッキングが行えるようになっている。
現在は、この電子倉庫システムは開発機1台で稼働しているが、今後は工場全体に拡大し、省力化と省スペース化を進めていく計画だという。さらに、これらの情報は部品在庫データベースにリアルタイムで送られているが、この部品在庫情報をEMSの顧客などに公開していく。「EMSでは顧客が持ち込んだ指定部品などを使って生産する場合も多い。この持ち込み部品の数の把握などは、今までは電話やメールで人手を介してやりとりしてきたが、これらをリアルタイムで見えるようにする」(担当者)。
Copyright © ITmedia, Inc. All Rights Reserved.