トヨタの具体事例から見えてくる、データ動線整理の重要性:IIoTの課題解決ワンツースリー(8)(2/2 ページ)
産業用IoT(IIoT)の活用が広がりを見せているが、日本の産業界ではそれほどうまく生かしきれていない企業も多い。IIoT活用を上手に行うためには何が課題となり、どういうことが必要になるのか。本稿ではIIoT活用の課題と成果を出すポイントを紹介している。第8回では、「IoT活用に向けたデータ動線整理」について、トヨタ自動車の工場へのSCADA(Supervisory Control And Data Acquisition)導入事例を通して解説したい。
将来的な全体最適化を実現するための、データの動線整理
どのSCADAを導入するとしても、工場全体の最適化を目指すためのIIoTプラットフォームとしての活躍を期待するのであれば、データを一元的に集約する動線を整理し、再構築することが重要となる。トヨタもこの点に着手する必要があった。
改善前のトヨタの工場内のデータ動線について、少し解説しよう。約800台のロボットをはじめとする設備は工程ごとにPLC(工程PLC)に接続され、設備のデータはまず工程PLCに集約される。アンドン表示のための一部のデータがアンドン用のPLCに送られ、可動管理や品質管理のためのデータは専用サーバに送られるなど、個別の目的に部分最適化された動線が複数敷かれていた。すなわち、各工程PLCに集まったデータの全てを収集し、保存するセクションがない状況であった。
そこでトヨタは、SCADAの導入に伴い、各設備および工程PLCのデータを直接に集約するフラットな動線を再整備した。個別の目的に応じて集めるデータを絞るのではなく、まずあらゆるデータを一元的に集め、アウトプットの際に使用するデータを選別するという順序に改めたのだ。工場に存在する全情報を収集・保存・解析し、モニタリングや工程の全体最適化のために活用できる状況が整えられた。
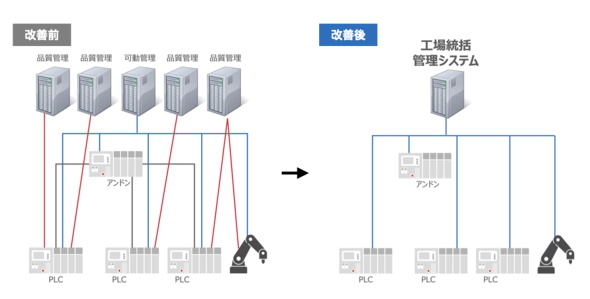
SCADA導入前のデータ導線(左)と導入後のデータ導線(右)。改善前は赤、黒、青の動線で異なるデータを送受信していたが、改善後は全てのデータが統括管理システム(SCADA)で収集されることになった[クリックで拡大] 出所:リンクス
そのアウトプットの一つとして、先述したアンドンについてもWeb化が進められ、工場内外のどこにいても、いつでも設備の状況や解析結果が手元のタブレット端末やスマートフォンで確認できるようになった。
「アンドンの掲示場所まで表示を見に行き、現場に向かい、対応内容を決め、人と機材を集めに戻り、対応し、手書きで記録し、後日報告する」という時間と労力をかけて行っていた作業は「設備に一番近い担当者がタブレット端末に表示されたトラブル内容と対応作業内容を確認。迅速に対応し、その作業内容はデジタルデータとして自動で蓄積・共有される」という形になり、状況把握のスピードは格段に向上した。
記録できていなかった秒単位での設備稼働履歴もリアルタイムで残るようになった。これらのデータを解析することで設備の老朽状況なども見えてくるだろう。大規模な工程停止につながるようなトラブルを未然に察知し、生産に影響しないようなメンテナンス計画を策定できるだけでなく、保全担当者を常時スタンバイさせておく必要がなくなる。データを現状の把握だけでなく、兆候管理に生かすことで、人的負担の軽減にもつながっていくことが見込まれる。
今後の取り組みについて「他工場への展開と、さらなる機能拡充を目指したい」と同グループの下西隼人氏は展望を語った。まずはIIoT化を他工場にも展開し、各工場の比較を通して新たな知見を見つけ出していきたいという。「SCADAの導入によって、これまで設備のデータを見ることのなかった人もデータにアクセスできるようになった。現場にはない新しい視点が加われば、SCADAの機能拡充や工程改善がさらに進められる」と下西氏は意気込む。既にエネルギー消費量や品質情報、メンテナンス情報の可視化を図り、相関の解析も進んでいるとしている。
SCADAの本領は、新たな知見の発掘と活用にあり
トヨタのように、早く、安く、高品質な製品生産を実現したい企業は少なくないはずだ。そういった企業の工程改善においてSCADAは強力な武器になり得るが、その本領を発揮させるためにはデータ動線の整備が欠かせない。しかし、ひとたび動線を整えたならば、部分最適化されていたシステムの機能を損なうこともなく、会社全体の生産体制改善につながるデータプラットフォームの構築を実現できることを、トヨタの事例は示している。
日本の産業IoT活用事例はまだ多くなく、導入検討の際に参照できる情報が少ないのも実情だが、同社の取り組みの広がりが、国内でのIIoT普及の起爆剤になることに期待を寄せている。
本稿では、2019年のトヨタの事例を基に、工場のIoT化の具体的な進め方や、その過程で意識・解決すべき「データの動線整理」について紹介した。トヨタでは2019年の「Industrial IoT Meeting」での発表から現在に至る2年間で、さらに機能開発を進めている。次回は成果事例の一部として、データのクラウド連携や工場内の電力消費の可視化といった新規機能について、その内容をお届けしたい。
著者紹介:
リンクス 代表取締役 村上 慶(むらかみ けい)
1996年4月、筑波大学入学後、在学中の1999年4月、オーストラリアのウロンゴン(Wollongong)大学に国費留学、工学部にてコンピュータサイエンスを学ぶ。2001年3月、筑波大学第三学群工学システム学類を卒業後、同年4月、リンクスに入社。主に自動車、航空宇宙の分野における高速フィードバック制御の開発支援ツールであるdSPACE社製品の国内普及に従事し、国内におけるトップシェア製品となる。2003年、同社取締役、2005年7月、同社代表取締役に就任。
Copyright © ITmedia, Inc. All Rights Reserved.
関連記事
全ての始まりは「データの標準化」から、IIoT基盤に求められる役割と機能
産業用IoT(IIoT)の活用が広がりを見せているが、日本の産業界ではそれほどうまく生かしきれていない企業も多い。IIoT活用を上手に行うためには何が課題となり、どういうことが必要になるのか。本稿ではIIoT活用の課題と成果を出すポイントを紹介している。第7回では、IIoT活用に必須の「データの標準化」と、これに対するIIoTプラットフォーム活用のポイントを解説する。SCADAはIIoTソフトウェアプラットフォームへ進化、その実態に迫る
産業用IoT(IIoT)の活用が広がりを見せているが、日本の産業界ではそれほどうまく生かしきれていない企業も多い。IIoT活用を上手に行うためには何が課題となり、どういうことが必要になるのか。本稿ではIIoT活用の課題と成果を出すポイントを紹介する。第2回では、IIoTソフトウェアプラットフォームの役割を果たすSCADAの特徴について紹介する。スマート工場は“分断”が課題、カギは「データ取得」を前提としたツールの充実
工場のスマート化への取り組みは2020年も広がりを見せているが、成果を生み出せているところはまだまだ少ない状況だ。その中で、先行企業と停滞企業の“分断”が進んでいる。新型コロナウイルス感染症(COVID−19)対応なども含めて2021年もスマート工場化への取り組みは加速する見込みだが、この“分断”を解消するような動きが広がる見込みだ。スマートファクトリー化がなぜこれほど難しいのか、その整理の第一歩
インダストリー4.0やスマートファクトリー化が注目されてから既に5年以上が経過しています。積極的な取り組みを進める製造業がさまざまな実績を残していっているのにかかわらず、取り組みの意欲がすっかり下がってしまった企業も多く存在し2極化が進んでいるように感じています。そこであらためてスマートファクトリーについての考え方を整理し、分かりやすく紹介する。エッジは強く上位は緩く結ぶ、“真につながる”スマート工場への道筋が明確に
IoTやAIを活用したスマートファクトリー化への取り組みは広がりを見せている。ただ、スマート工場化の最初の一歩である「見える化」や、製造ラインの部分的な効率化に貢献する「部分最適」にとどまっており、「自律的に最適化した工場」などの実現はまだまだ遠い状況である。特にその前提となる「工場全体のつながる化」へのハードルは高く「道筋が見えない」と懸念する声も多い。そうした中で、2020年はようやく方向性が見えてきそうだ。キーワードは「下は強く、上は緩く結ぶ」である。工場自動化のホワイトスペースを狙え、主戦場は「搬送」と「検査」か
労働力不足が加速する中、人手がかかる作業を低減し省力化を目的とした「自動化」への関心が高まっている。製造現場では以前から「自動化」が進んでいるが、2019年は従来の空白地域の自動化が大きく加速する見込みだ。具体的には「搬送」と「検査」の自動化が広がる。