オムロン逆転の発想、「カイゼン」と「省エネ」は同じことだった:小寺信良が見たモノづくりの現場(3)(5/5 ページ)
生産のQCD(品質、コスト、納期)を見直すカイゼン活動は、現場力の見せ所だ。一方、省エネはこれまで現場から離れた工場の管理部門の役割だとされてきた。QCDと省エネを同じ目線で捉えると何ができるのだろうか。オムロンの事例を小寺信良が紹介する。
リフロー炉の大きな温度変更が不要に
もう1つは、温度管理(温度プロファイル)の見直しである。草津工場では少量多品種生産のために、頻繁にラインの変更が起こる。このときに問題になっていたのが、ラインを切り替えると温度管理を変更するために時間がかかることだ。
例えば接着で処理する機器の部品は、耐熱温度が比較的低い。一方リフロー炉によるはんだ付け機器の部品は、耐熱温度が高い。従来はリフロー炉用の温度から接着材用の温度まで120℃下げるために、時間がかかっていた(図8)。
そこで、部品の耐熱温度を検証してみた。すると実際には、接着処理の部品に低耐熱品は使用していないことが分かった。ということは、接着プロファイルへの切り替えのため120℃も下げるまで待つ必要はなく、40℃だけ下がれば作業に取り掛かれる。これにより、ライン切り替え時の温度変更時間を、毎回短縮できた。
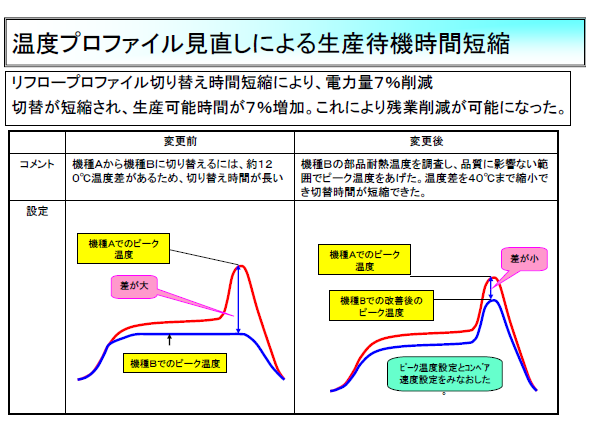
図8 温度プロファイルの見直しによる効果 温度を120℃下げて、安定するまで毎回待機していた(図右)。しかし、調査の結果、耐熱温度が低い接着剤は使用しておらず、温度低下の幅が40℃と少なくても構わないことが分かった。これだけで待機時間を短縮できた。
電気代はもちろん、生産効率の向上という面で何倍もの成果が上ったことになる。勤務時間内に全ての製造が終わり、残業も減る。働く人もうれしい。そしてこれも、電力をモニターしていたからこそ、気付いたポイントだ。要するに温度を下げるために電気を切って一体何を待っているのだ? というところを発見できたからである。
誰に、どう見せるのか
電力の見える化は、今に始まったことではなく、以前からもよく提案されてきた。オムロンが大きな成果を上げられたのはなぜか。それは、見える化だけでは駄目で、どうやって見せるか、誰に見せるか、というところがポイントだったのだろうと思う。
今後オムロンではこの取り組みをベースに、「環境あんどん」というシステムを作って、商品化していくという。突然“あんどん”などという言葉が出てきて面食らうかもしれないが、ここでいう「あんどん」とは、トヨタ生産方式で広がった手法の1つで、生産ラインごとに設けられている掲示ランプを指す。ラインに問題があったときに“あんどん”を各自が点灯して、異常発生を他者に知らせるためのものだ。
環境あんどんは、電力計をはじめ各種センサーのデータをリアルタイムで集約し、さまざまな切り口で電力環境を見える化するシステムである(図9)。例えば棟単位、フロア単位、部署単位、ライン単位、装置単位、ヒーター単位といった具合に、鳥瞰(ちょうかん)から細部までスケールを自由に変更して電力を見ることができる。

図9 環境あんどんの表示画面例 数値情報として時間ごとの消費電力量(kwh)、生産量と消費電力量の関係、パーティクルセンサの出力、温湿度、エア流量などが示されている。アラート画面は円を4分割した単純な表示が並んでおり、室内の異なる位置の情報が分かる。パーティクル、温湿度、エア、電力を示している。普段はアラート画面を見ていて、異常時に数値を見るという使い方だ。綾部工場での利用例。
現場にはさまざまなレベルでものを見ている責任者がおり、それぞれ自分が管理するスケールで、電力状況を見ることができるというのがポイントだ。これによって、次に手を付けるべきアクションが、担当者レベルで見えてくるというわけだ。
実際に草津工場での取り組みを見て感じたのは、「見える化すると楽しい」ということである。遊んでいるのか、と思われるかもしれないが、選抜メンバーが例えば「省エネ推進員」の腕章を付けて、目を三角にして構内を点検して回るような活動よりも断然よい。実践している人たちが、楽しそうなのだ。
それは、これまで見えていなかったエネルギー利用の時間軸と、製造ラインから得られる時間軸データを突き合わせて、一体何が起こっているのかを考える作業が、パズルを解く快感に似ているところがあるからなのではないか。楽しくないと、こういう取り組みは継続しない。目視に頼った見回りだけでも、一時的には省エネできるかもしれないが、定着せずそのうち元に戻ってしまうケースは多かっただろう。
エネルギー効率の最大化とは、製造現場のビジョンと一致する。さらには、QCDの概念とも相反しない。日本のモノづくりは、エネルギー効率の視点から見ていくことで、もう一歩次のステップに進むことができそうだ。
【修正履歴】 記事公開後に図1〜図9をより高解像度のものなどに差し替えました。一部、図の表現内容が変わっています。4ページ第10段落にあった生産リードタイムに関する表現を改めました(2013/3/29)。5ページ第1段落から第4段落の温度管理に関する表現を改めました(2013/3/30)。
筆者紹介
小寺信良(こでら のぶよし)
映像系エンジニア/アナリスト。テレビ番組の編集者としてバラエティ、報道、コマーシャルなどを手掛けたのち、CGアーティストとして独立。そのユニークな文章と鋭いツッコミが人気を博し、さまざまな媒体で執筆活動を行っている。
Twitterアカウントは@Nob_Kodera
近著:「USTREAMがメディアを変える」(ちくま新書)
Copyright © ITmedia, Inc. All Rights Reserved.
関連記事
ソニーの“プロ機”が日本人にしか作れない理由
日本のモノづくりが失墜しているって? とんでもない。日本でなくてはできない価値のあるモノづくりの現場が、静岡にある。グローバル企業として生き残るには――ボッシュ栃木工場に見るニッポンクオリティ
自動車の品質とコストを支えているのは誰か。多くの部分を下支えしているのが部品メーカーだ。自動車部品メーカーの1つ、ボッシュ。その栃木工場の工夫を、小寺信良氏の目を通して語っていただいた。品質向上への努力とはどのようなものなのかが分かるだろう。白物家電を人手で1個ずつ作る日立――国内工場でなぜ
大量生産品であれば中国など海外の製造拠点を使う。最先端の製品でなければ、このような取り組みが一般的だろう。日立アプライアンスは白物家電や環境家電でこれとは全く逆の方針を採っている。茨城県の多賀工場で生産し、さらに1個ずつ手作業で作っている。なぜだろうか。どうしたらこのようなことが可能になるのだろうか。小寺信良が報告する。