良品作りのリフロー炉の操作方法と現場の人材育成方法(3):量産現場における良否の判定方法(2/3 ページ)
はんだ付けに用いるリフロー炉の操作方法や、実装ラインの品質を管理する現場の人材育成の手法を解説する本連載。第3回は、リフロー後のはんだの内部に気泡が残ってしまうボイドへの対策などについて紹介する。
2. 初期のボイド
フラックスは、熱反応の速いもの、鉛はんだ用のフラックスの方が残渣の影響を抑えやすい。特にボイドが問題になる部品は、熱的条件が許すのであれば、1回目のリフロー時はその部品のみ搭載せずにリフローし、2回目のリフロー時に固形分の少ない液状のフラックスを塗布した後で部品を搭載してリフローすることで、ボイド対策することができる。その際に使用するフラックスは、残渣が少なく、活性の弱いもので十分である。部品下に残渣が残りやすい、耐熱性の高いフラックス(溶剤)は問題を起しやすいので、従来の鉛はんだ用のフラックス(溶剤はIPAのみ)が適している(図6)。
3. ボイド対策実験(2)
通常、アルミ電解コンデンサはリードの大半が部品の下にあり、かつリードが細いので、上部ヒータの熱が伝わりにくく、また熱はコンデンサ本体に伝わるので、はんだの熱対流が十分に起こりにくくなる。そのため、より多くの熱を供給する傾向にあるがそれがかえってフラックスの劣化を進行させ、ぬれ性とともにはんだの流動性もさらに阻害されてボイドが発生しやすくなる。
設計的には、リードよりもランド幅を広く長くして、部品本体より外側に伸ばし、はんだ面がより多く上部ヒーターの熱を得られるようにする。同時に、はんだの熱対流が部品下側から外側にまで広がり、部品下のガスを放出し、またはんだ量を多くすることでフラックス量も増えるので、ぬれ性やはんだの流動性も改善されボイドが軽減される。リフロー炉の操作では特に下部ヒータを高くして、基板を通して部品下から熱を直接ランドに供給することによって熱不足とフラックスの劣化を同時に改善し、ボイドの発生を抑える(図7)。
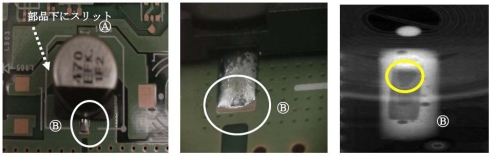
図7 (左)マスク開口が狭く、赤目が発生している(中央)プリヒートが少し長く、フラックスが劣化気味である(右)一部ボイドあり。部品下に大きなスリットがあるので、下部から熱風が吹き付けフラックスの劣化を早めている。こういう場合は、下部ヒータのファン回転数を落とすなどして、熱風によるフラックスの劣化を抑える必要がある(クリックで拡大)
スペース的に許されるのであれば、広めのベタランドにして不要な部分をレジストで覆い、下部からの熱供給を多くすることも対策になる(図8)。
はんだ量が多いと引っ張り強度が強くなり、これを剥がすと部品やランドが破壊・剥離してしまう。
図9は、再度、基板のスリットを耐熱テープで塞ぎリフローしたもので、 ボイドは減少している。
また図10は上記の電解コンデンサの基板のスリットを塞ぎ、下部の熱風の影響を抑えた状態の写真で、ここではフラックスの劣化が抑えられてボイドは減少している。
今回はあくまでもラフな実験であり、多層基板設計の影響が十分反映されてはいないが、おおむねフラックスのボイドに対する効果は確認することができた。実際には基板設計やリフロー炉の特性等の制約を受けるので、一概に同じ効果が得られるとは限らないが、動画での実験データと同じ傾向にある。
Copyright © ITmedia, Inc. All Rights Reserved.