良品作りのリフロー炉の操作方法と現場の人材育成方法(2):量産現場における良否の判定方法(3/3 ページ)
はんだ付けに用いるリフロー炉の操作方法や、実装ラインの品質を管理する現場の人材育成の手法を解説する本連載。第2回は、第1回に引き続き、実装ラインにおけるはんだ付けの良否について、具体的な事例を紹介する。
3. 事例(5)遠赤外線によるボイドの削減効果
図6は、遠赤外線によるボイドの削減効果を見るために、エアのみによる加熱のリフロー炉と、エアと遠赤外線で加熱するリフロー炉を比較したものである。
遠赤外線効果で基板自体が発熱し、フラックスが劣化せず、その効果で部品下のはんだの熱対流でガスが放出されている。また、フラックス効果で、溶融したはんだが熱対流を起し、発生したガスがフィレットから放出されてボイドが改善される。
図7は、上記実装品のX線観察である。N2がなくても、フラックスを選ぶか、あるいはフラックスを劣化させなければ、溶融中のはんだの熱対流によってガスはボールの外に放出され、ボイドは抑えられる。耐熱性の高いフラックスでガスの発生を抑えるよりも、遠赤外線のコントロールによって、熱反応の速いフラックスでガスの放出を促進させる方が効果的である。
また、大気リフローでもフラックスを劣化させなければN2や強い活性剤は特に必要ない。なお、オムロン草津の実験報告によると、リフロー炉におけるランニングコストの内N2発生にかかるエネルギーコストは、年間約200万円で、ランニングコスト全体の66%を占めるとされている。オムロンでは、実装ラインでの年間のエネルギーコストの見える化を、各種センサを用い、データとして収集している。
プリヒートで過剰な熱を供給すると、基板が蓄熱して冷却速度が遅れ、強いデンドライドが現れる。これはフラックスの劣化を意味しているので、フィレット光沢が失われている場合や、フィレット表面になめらかさがないことは、同時にボイドが発生していることを意味する(図8、図9)。
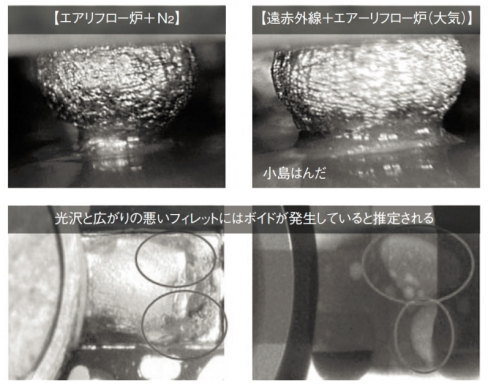
図8 ボイドの発生しやすいアルミコンデンサを遠赤外線リフローで実装したが、下部ヒータを高くしても、アルミには遠赤外線による熱影響がほとんどない。部品下のフラックスに対しては、基板の自己発熱からの熱が供給されるため、リードの大半が部品の下にあっても熱不足が起こる心配はない(クリックで拡大)
部品によっては、一見しても問題がないように見えるため、全体のフィレット形状、光沢、なめらかさを観察するようにする。特に、フラックス残渣の荒れ具合は観察のポイントになるので、最終的には消去法で判断する。
フラックス効果が失われると、はんだのぬれ上がり(部品吸着)不足でリードとランド間のはんだが厚く残ってしまう。はんだの流動性が失われるのため、ガスがボイドとして残ってしまう。本来、フラックスの効果は、部品リードをぬれ上がる力が部品リードを基板側に吸着するものなので、リードとランドの間にはんだはほとんど残らない(図10)。
図11中の右の写真では、リード部品の熱もリードからランドに直接伝わり放熱されている。
量産現場では、基板上のすべてのポイントのボイドを検査するのは生産効率上、無理であり、現実的ではない。ラインを止めず、すばやく製品の良否や温度プロファイルの適否を判断するためには、上記した(および前回の)事例の外観観察による判断が一番効果的で効率が良い。それと同時に、現場の人材育成も、マイクロスコープを用いることによって比較的短期間(2〜3カ月)で行うことが可能である。
製造装置(リフロー炉)も検査装置(マイクロスコープ)も、その操作方法や観察方法が付随していて、初めて効果を得られるものであり、ただ単に数的性能を追いかけても、投資が増えるのみで、費用対効果が得られない。
現場の教育にはロータリーレンズを用い、作業者には動画や静止画などで観察の角度を変えながら、全体像の変化を理解させることが重要である。実際に、(株)ハイロックス製のマイクロスコープを導入したことで、部品点数での不良率を1ppm以下に改善できたという事例が増えてきている。また、特筆すべきことは、不良率10ppm以下になると、不良の発生箇所なり原因が、現場で解析できるようになることである。この効果は非常に大きいものである。
Copyright © ITmedia, Inc. All Rights Reserved.
関連記事
良品作りのリフロー炉の操作方法と現場の人材育成方法(1)
プリント基板に電子部品を取り付ける実装ラインで、製造コストを抑えながら品質を確保することは容易ではない。本連載では、はんだ付けに用いるリフロー炉の操作方法や、実装ラインの品質を管理する現場の人材育成の手法について、具体的な実例を挙げながら解説する。「熱する・溶かす・流す」はんだ付けの極意
今回は、はんだ付けの手順・ポイントを紹介しながらプリント基板に部品を取り付け、「H8Tiny-USB」を完成させる