ダイハツ「ミライース」、37.0km/lを超えられる新型エンジンをなぜ諦めた?:ミライース 開発者インタビュー(1/4 ページ)
先頃フルモデルチェンジされたダイハツ工業の軽自動車「ミライース」。開発陣に量産までのいきさつを聞くことができた。驚異の軽量化と安全装備の充実を両立しながら、価格を抑える工夫はどのようにして生まれたのか。そこにはミライースを利用するユーザーへの思いにあふれていた。
新型「ミライース」の試乗記編はこちら ⇒ 新旧「ミライース」乗り比べ、走って見えてきたダイハツの取捨選択と企業努力
冗談かと思うほどのむちゃな要請「730kgのクルマをさらに軽くしろ」
まずはダイハツ工業 車両開発部ボデー設計室の二星勲生氏に担当部署での開発の苦労話を聞かせてもらった。
二星氏 私は先代モデルからボディー設計を担当していたんですけど、その時もベースのミラからかなり軽量化していたんですよ。そこからさらに80kg軽量化しろというんですから、最初はウソかと思いました(笑)。
高根氏 開発の最初から車両重量の数値目標があったのはなぜか。それはやはり、あのライバルメーカーへの対抗策なのか。
二星氏 浜松のメーカーさんが650kgで作ってきたものですから。われわれとしては驚きだったんですよ、650kgでクルマが作れるのか! と。われわれもそこにターゲットを置きまして、650kg目線で開発を行ってきました。単に質量を減らすだけなら簡単なんですけれど、性能は低下させちゃいけない。もう、非常に苦労しましたね。
高根氏 そもそも軽量化した軽自動車をさらに80kg軽くするのは尋常な開発ではない。
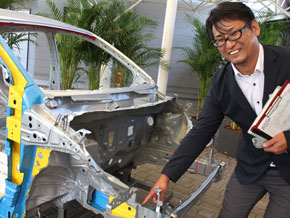
ダイハツ工業 車両開発部 ボデー設計室主任の二星勲生氏。先代と新型の二代に渡ってミライースのボディー設計を行った。「ここもスーパーハイテンを使っていますが、軽量化のためにレーザー溶接しています」(クリックして拡大)
二星氏 軽自動車でもベーシックなクルマですから、スッピンのクルマをさらにスッピンにしなくちゃいけないってことなんです。素うどんから何を取ったらいいんだろう……と。うどんを取ったらうどんじゃなくなるし……。
高根氏 大阪の企業だけに、例えにうどんが出てくる。走りの質感を高めながら軽量化もしろ、というのは“素うどん”じゃなくて具を入れろ、でもカロリーと価格はそのままで、みたいなものではないか。
二星氏 素うどんでもおいしくなければ、お客さんに満足してもらえません。そういう意味では普通のクルマの開発より苦労しましたね。
高根氏 素うどんとしての基本骨格にはレーザー溶接、ホットスタンプのスーパーハイテン材…5年前なら考えられないほど、ぜいたくな製法を駆使して作られている。
二星氏 これらは「タント」で導入していたからミライースでも利用することができました。フロアパネルなどはスポット溶接とレーザー溶接を組み合せています。スポット溶接ではパネルをつないでも重なる部分ができてしまうので、突き合わせで溶接できるレーザー溶接を使いました。これも剛性を確保した軽量化対策なんです。
高根氏 レーザー溶接は溶接面積が大きくて剛性が確保しやすいだけでなく、重なった部分がないためグラム単位で確実に軽量化できるというのは確かにその通りだが、生産性はスポットより確実に落ちるはずだ。フロントメンバーは、前端にハイテン材をつなぐため、メンバーをグルリとレーザー溶接していると聞いた。一方で、静粛性を高めるためにボディーパネルの穴を減らしたと発表しているが、ドアなどに制振鋼板などは使っていないのか。
二星氏 その辺は普通の鋼板です。ドアに限らずあらゆる穴を見直して「この穴、ホンマに要るんか?」というところからやりました。生産性の都合で空いている穴もいろいろあるんですね。「この穴なくされへんのか、もっと小さくしてもイケるんやないか」って。
高根氏 軽量化のための穴もあるのではないか。
二星氏 それもあるんですよ。でも、空け過ぎるとやっぱり室内に騒音が透過してしまうので。空ける部分、空けない部分、適材適所にこだわりました。
Copyright © ITmedia, Inc. All Rights Reserved.