日本に2カ所しかない電磁波耐性試験設備、OKIエンジニアリングが導入:車載電子部品(1/2 ページ)
OKIエンジニアリングは、設備の増強を行って「カーエレクトロニクス テストラボ」として試験体制を強化した。先進運転支援システム(ADAS)やコネクテッド化、パワートレインの電動化によって電子機器の搭載が増加し、EMC試験や信頼性評価の重要性が高まっていることに対応した。
OKIエンジニアリングは、自動車向けのEMC試験や信頼性評価で、2020年までに売り上げの倍増を目指す。先進運転支援システム(ADAS)やコネクテッド化、パワートレインの電動化によって電子機器の搭載が増加し、EMC試験や信頼性評価の重要性が高まる。サプライヤーが単独では導入できない設備も必要となるため、受託試験の需要が拡大する。2018年には、2012年比で受託試験件数が倍増する見通しだ。
2016年末には既存の設備での稼働率が100%を超えていたため、設備の増強を行って「カーエレクトロニクス テストラボ」として試験体制を強化した。「日本国内では他社含めて2カ所目」(OKIエンジニアリング)という新しい設備や、大型の部品の信頼性評価に対応した設備を導入。これまで増加していた試験の待ち時間を短縮するとともに、今後の需要増に対応していく。
電子部品からバンパーまでカバーする試験設備
カーエレクトロニクス テストラボは、OKIの本庄工場(埼玉県本庄市)内に設置した。2017年4月13日から稼働している。面積は1500m2。本庄工場にはOKIエンジニアリングのシステム評価事業部とEMC事業部がある。
OKIエンジニアリングは本庄の拠点に2007年に車載電波暗室を設置して以来、需要に応じて車載向けの評価設備を増やしてきた。毎年さまざまな種類の環境試験設備を導入している他、2016年には車載電波暗室を2つ増設。合計4つの車載電波暗室は同一の仕様とし、再現性の高い試験データを提供するとしている。
また、2016年には「日本国内では他社含めて2カ所目」(OKIエンジニアリング)という、電磁波耐性試験を行う「リバブレーションチャンバー(反射反響室)」も設置している。
バンパーやドアのような大型部品に対応できる評価設備もそろえている。従来、OKIエンジニアリングでは電子部品やECU、カーナビゲーションシステムなどサイズが小さな部品を対象に評価試験を行ってきたが「1つ1つの電子部品の信頼性を確認できても、組み立て後も同じように信頼性が確保できているのか、という点を自動車メーカーが重視するようになってきた」(OKIエンジニアリング)。
大型部品に対応しているのは、潮風などによる塩害を想定した塩水噴霧試験機や、直射日光が当たる環境を再現した恒温恒湿室、リバブレーションチャンバーなど。恒温恒湿室は耐荷重1トンまで対応している。クルマを丸ごと持ちこめる電波暗室もある。
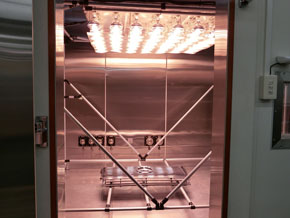
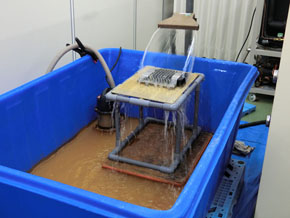
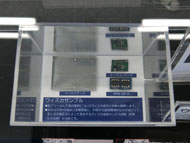
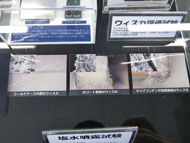
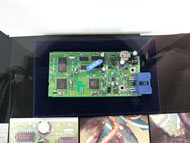
OKIエンジニアリングにとって、自動車向けの受託試験は年平均12〜14%の成長を続ける重要なビジネスだ。自動車向けが年々右肩上がりとなる一方で、設備・人員ともに試験の拡大に対応するのが難しくなっており、ピーク時には昼夜2交代制で対応していた。
カーエレクトロニクス テストラボは、設備を増強しただけでなく人員も増やす。新卒や中途での採用、OKIグループ内からの派遣によって、2017年度は2015年度比で10%増員する。
Copyright © ITmedia, Inc. All Rights Reserved.