自動車の電子化を支える適合プロセス、ツール活用が鍵に:いまさら聞けない 適合プロセス入門(後編)(2/2 ページ)
車載システムを開発する上で重要な役割を果たす「適合プロセス」。適合プロセスの重要性を説明した前編に続き、後編では、車載システム開発における適合プロセスの変遷や適合プロセスに用いるツールについて解説する。加えて、「バーチャル適合」をはじめとする将来技術も紹介しよう。
適合プロセスの今後
これまでの適合プロセスを俯瞰(ふかん)すると、テストベンチや実車での適合にどうしても寄り掛かってしまっていることが分かります。これをもう少し初期段階に移行するとともに、シミュレータの精度を上げて適合を行えるようにするための取り組みが「バーチャル適合」になります。
また、従来のテストベンチや実車による適合作業は、技術者が直接手を動かす要素が多いこともあってか、ある意味「技能伝承」であったり、ルーチンワークな側面が多かったりします。これを、ナレッジマネジメントの観点から、適合プロセスを捉え直したツールも存在します。
これらの新たなツールの活用によって、適合作業の前倒しが可能になります。
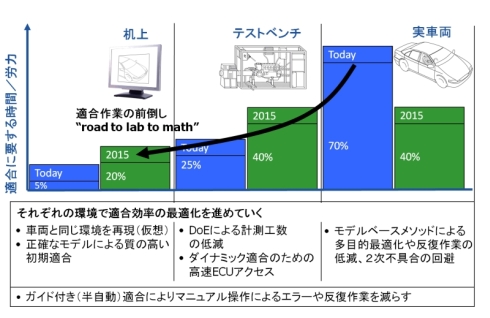
ツール活用による適合作業の前倒しのイメージ。現在は、実車を用いた適合作業が大半を占めているが、ツールの活用が進めば、机上でのバーチャル適合や、テストベンチを用いた適合作業の割合が増加するという。(クリックで拡大) 出典:イータス
バーチャル適合
制御モデルを各種の制御モデリングツールで作成するのは「車載システム開発の適合プロセスに用いるツール」の項で述べた通りです。「制御モデル」に加えて、それらの「入」と「出」の振る舞いがある程度決まれば、適合作業は行えます。この「入」と「出」についても、「センサー」と「アクチュエータ」のようにモデリングすることが可能です。このモデルは「プラントモデル」と呼ばれています。
つまり、「制御モデル」+「プラントモデル」が定義できれば、ECUをPC上というバーチャルな形で再現できるわけです。もちろん、適合プロセスについても、テストベンチや実車を用いる場合と同様に、キャリブレーションツールを用いたバーチャルな適合作業を行えるようになります。
動的な適合処理と高速化
現在のECUの適合プロセスに用いられている通信プロトコル「ASAP3/MCD-3」は、適合作業中も計測する動的な適合処理を行うことができません。これは、適合作業中はプロトコルを遮断(ブロッキング)するという仕様によるものです。また、伝送速度そのものも遅いので、その間にターゲットの状態が遷移してしまうことも問題になります。
そこで、適合プロセスにおいて、ブロッキングをなくし伝送速度を上げて、連続的にターゲットの状態を監視できるような新しい方式がいくつか提案されています。これによって、エミッションピークや不安定エリアを回避できるようになり、計測時間の短縮、エンジンの損傷リスクや負荷を低減できます。
モデルベース適合
実験計画法(DOE)に基づいた適合プロセスの1手法です。モデリングツールの多くがこの機能を有しています。パラメータの最適値を自動で求めたり、出来上がったモデルからキャリブレーションデータをエクスポートできたりします。最終的には、このエクスポートしたデータを用いて、実車との比較ができるようになります。
ナレッジマネジメント
適合プロセスに携わるオペレータやエンジニアは多忙です。ルーチンワークに忙殺され、発生した不具合に対応しにくくなる事態も考えられます。適合プロセス業務のルーチンワークを自動実行するツール(ETASの「CaliAV」など)を用いれば、オペレータやエンジニアが本来行うべきはずのクリエイティブな業務に集中することが可能になります。自動実行時にガイド表示も行われますので練度の低いオペレータやエンジニアの教育用途にも適用可能です。
もはやツールなしに適合は行えない
筆者自身が適合ツールを手掛けていたころから10年以上が過ぎました。車載電装品も大きく進化しています。当時扱っていたのは、INCAの前身である「VS100」というDOSベースで動作するツールでした。顧客のところに訪問した時に、ある中堅のエンジニアが困惑した表情で言ったことを印象深く覚えています。「VS100とMicrosoftの『Excel』が若いエンジニアをダメにしたんだ」と。
その頃の適合業務は、ROMライターでDIPのEPROMにプログラムを焼き付けてデータの変更がある度に交換するのが一般的なスタイルでした。手描きのグラフを使うこともあったのです。そのような時代に、実車走行しながら、リアルタイムでデータを変更できるツールや、データを与えて最小二乗法などでさらっとグラフを描いてしまうソフトウェアは、今日でいうところの「破壊的なイノベーション」だったわけです。
「ROMを焼くのが面倒だから、考えてデータを組み立てる。グラフ作りは大変だから、リポートを吟味するんだ」。分かります、その気持ちは……。でも時がたち、複雑化した車載システムが相手では、もはや今回ご紹介したようなツールなしでは開発できなくなっています。大事なのは、ツールを使いこなして競争力のある製品をいち早く市場に投入することだと思います。
<取材協力・資料提供:イータス株式会社>
プロフィール
大橋 修(大宮技研合同会社 エグゼクティブエンジニア、産業技術大学院大学)
日本精工(株)でエアバッグの制御ソフトウェア開発、ボッシュ(株)にてエンジンマネージメントシステム開発、適合ツールの開発・サポート、プロジェクトマネージメント、ノキアにてシンビアンOS用ミドルウェアS60の開発や画像処理の研究などを担当。その後、外資系半導体会社勤務を経て現職。原稿執筆、システム開発、コンサルテーション業務を行う。
Copyright © ITmedia, Inc. All Rights Reserved.
関連記事
日本の自動車メーカーの強さ、その源泉は「適合プロセス」にあり
日本のモノづくりの衰退が叫ばれる中で、自動車産業は、世界市場で互角以上に渡り合う強さを維持している。この日本の自動車メーカーの強さを支えているのが、製品開発プロセスとしてあまり注目されることのない「適合プロセス」なのである。「機能安全」の導入で何が変わるのか?
自動車向けの機能安全規格ISO 26262の策定作業が最終段階に入った。この規格では、機能安全を実現し、それを証明するために必要となる開発プロセスが定められる。では、その新たな開発プロセスは、従来の開発プロセスとどのように異なり、それを適用する際にはどのようなことが課題になるのだろうか。本稿ではまずこの点を明らかにする。加えて、機能安全を実現する上でポイントとなるマイコンについて、各メーカーの取り組みの様子を紹介する。AUTOSARで変わる車載ソフトウエア開発
車載ソフトウエアの標準規格AUTOSARの採用に向けた活動が活発化している。規格策定の中心地となっている欧州では、AUTOSAR準拠の車載ソフトウエアを採用した新車が発売されるなど、取り組みが先行している。一方、AUTOSARへの対応が遅れていると言われていた日本でも、JasParの評価活動をはじめさまざまな取り組み事例が報告されるようになった。本稿では、まず既存の車載ソフトウエアとAUTOSAR準拠の車載ソフトウエアの違いについてまとめる。その上で、欧州と日本におけるAUTOSARの実装に向けたさまざまな取り組みを紹介する。