AIとCAE、ビッグデータの融合で匠の技は残せるのか――オムロンのチャレンジ:設計者CAE(1/2 ページ)
オムロンは1980年代からCAEの活用環境を整備してきた。さらに今、取り組もうとしているのが、ビッグデータおよびAI(人工知能)とCAEの融合だ。将来は実測とCAEを一致させることによる最適な設定などが自動で可能になるとする。さらに、この取り組みによって職人の技術を可視化して、後世に残していくことができるのではないかと考えているという。同社でCAE業務を推進するオムロン グローバルものづくり革新本部 生産技術革新センタ 要素技術部の岡田浩氏に話を聞いた。
オムロンは1980年代からCAEの活用環境を整備してきた。さらに今、取り組もうとしているのが、ビッグデータおよびAI(人工知能)とCAEの融合だ。将来は実測とCAEを一致させることによる最適な設定などが自動で可能になるとする。さらに、この取り組みによって職人の技術を可視化して、後世に残していくことができるのではないかと考えているという。同社でCAE業務を推進するオムロン グローバルものづくり革新本部 生産技術革新センタ 要素技術部の岡田浩氏に話を聞いた。
主力のFA機器をはじめ全社でCAEを活用
オムロンは制御機器およびファクトリーオートメーション関連機器を主力としている。センサーやスイッチなどのFA機器製造からスタートした経緯もあり、今もその売り上げが半分を占める。また健康機器にも注力している。近年はIoTを活用した生産現場のデータの見える化および故障予知などにも取り組むとともに、人と機械の協調を目指した取り組みも行う。
オムロンは約30年前、1980年代後半からCAEを導入、業務に活用してきた。同社のCAEに関する技術開発や社内展開は、社内全体にまたがる組織「開発プロセス革新センタ」と「生産技術革新センタ」の業務の一環として行われている。かつてはCAEの専門家が集まる組織が設置されていたが、CAEの業務を請け負うだけの形になってしまい、設計、製造現場と協調して課題を解決できる体制からは程遠かった。そこで専門組織を解体して今の形に落ち着いたという。
開発プロセス革新センタでは、主に設計上流において、試作の代替としてCAEを活用し、製品使用時の機能などを確認することで、開発期間の短縮を目指す。生産技術革新センタでは主に製造工程をカバーし、設計通りに製品を加工できるのかの確認や、新技術の導入前検討などを行う。また両者は独立して検討できないこともあるため、時には密接に連携しながら業務を進めている。
また両センタでは、CAEを効果的に導入できるタイミングを探るために各社内カンパニーの業務プロセスを分析したり、設計者自身がCAEを使うための工学的な基礎教育を行ったりしている。
このように、オムロンでは全社にわたって効果的にCAEを活用するための環境を構築してきた。最近の開発プロセス分野では連成解析に着目し、樹脂流動や熱、構造のトレードオフを検討している。また生産技術分野では品質向上に着目し、加工が製品の性能に与える影響を評価するための解析技術を構築している。
新成形技術の取り組みも
最近の生産技術分野における取り組みの1つは射出圧縮成形だ。この成形法は最近、自動車産業をはじめさまざまな業種で取り組まれている。粘度の高い樹脂を狭い型に流す場合、型全体にきれいに行き渡らせることが難しい。そこで、まず型を完全には締めない状態で樹脂を流した後に、完全に締めて成形を行う。薄くかつ大判化するタブレット内のシートなどにも使われている。生産技術CAEにおいては、CAEが使えるだけでなく、生産現場も熟知していることが重要になるという。
開発プロセス分野と生産技術分野が協力して取り組んだ例が、近接センサーだ。近接センサーは水や油に触れる環境で使用されるため、樹脂で封止されている。封止時には熱や樹脂の収縮が加わるため、事前に生産技術分野のシミュレーションを行う。また使用環境では、気温や湿度の変化によって、樹脂が収縮・膨張を繰り返す。そのため樹脂が剥がれたり、水が浸入したりしないよう、ヒートサイクルのシミュレーションも行う。生産現場で問題が発生した後にCAEで原因を探るのでは手戻りが大きくなるため、両者が連携して設計の上流から検討を行ったという。
AI・ビッグデータでリフロープロファイルを自動設計する
岡田氏は今、CAEにビッグデータおよびAIを利用する新たな取り組みを進めている。「まず取り組みたいのは、AIが得意とする画像処理」だと岡田氏は話す。具体的には基板に部品をはんだ付けする際に使用するリフロープロファイルの設定の自動化に取り組みたいという。
リフロー炉ではんだ付けを行う際は、基板にクリームはんだを塗布して部品を載せてから炉に入れる。その際、熱風の温度や流速を時刻ごとに設定した情報であるリフロープロファイルを用意する必要がある。
「しかし各部品によって、『何度を超えてはいけない』とか、『ある温度では何秒までなら大丈夫』など仕様はまちまちです。部品が壊れないよう配慮しつつはんだが溶ける温度にまで加熱する必要があり、炉の温度管理は非常に繊細かつ重要な作業です」(岡田氏)。
このプロファイルを決めるのは、まさに“職人技”だという。図2のように、熱電対を要所に取り付けて何度も温度を測定し、部品の耐熱条件を考え合わせてプロファイルを決定する。搭載部品の数は数百個になることもあり、かつ経験と勘が要求される分野だ。しかも最近は部品の小型化が進むとともに、複数の材料を組み合わせた新部品も登場し、難易度はますます高まっているという。
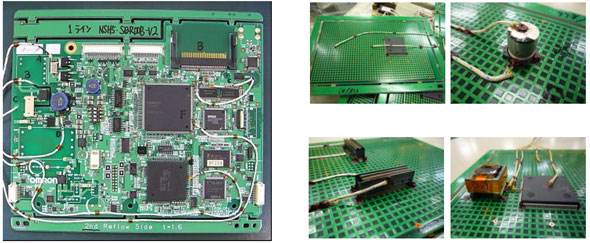
図2:温度を測定するための熱電対を付けた基板。現状ではリフロー炉内における各部の温度を実測してリフロー条件を導出している。これをAI、ビッグデータを用い基板の配線パターン・部品配置の画像データと各部品の情報を入力して簡略化させたいという。
そこでプロファイルの決定にAI、ビッグデータを活用する。「今まで蓄積してきた各部品・基板の温度データと、基板の配線パターンおよび部品配置の画像データがたくさんあります。これらを利用すれば機械学習は可能でしょう」(岡田氏)。
基板の配線パターンや使用部品の種類、各部品の材料の物性データ、リフロープロファイル、そして各部品の接合部の温度などを用いて学習させる。その上で入力値として新たな基板の配線パターン、部品配置の画像データ、実装する部品の種類や材料の物性値を与えることにより、リフロープロファイルを導き出すというわけだ。
Copyright © ITmedia, Inc. All Rights Reserved.