生産性はまだ向上する――理想と現実のギャップを埋めるPLMとMESの連携:モノづくり最前線レポート(30)
2011年9月7〜8日にボストンで開催された米シーメンスPLMソフトウェアのアナリスト・カンファレンスでChuck Grindstaff氏は、設計と生産、保守の間にあるギャップを埋める、と語った。その真意とは?
そのスキマ、何が欠けている?
現代のモノづくりにおいて勝ち残っていくためには、製品の複雑化、グローバル展開、さらなる生産性の向上、さらには革新的な製品開発を続けることへの対応を同時に求められる。設計部門内に閉じたPDMシステムから、より広範な領域をカバーするPLMシステムの導入がある程度進んだことで、この20年ほどの間、生産性は向上し続けているが、それもまだ経営者や市場の要求に照らすと十分ではないといえよう。何かが欠けているのだ。
シーメンスPLMソフトウェアではこうした課題に対して「Top Floor(エンタープライズ層)からShop Floor(オペレーティング層)までのAutomation(自動化)を図る」ことで、ギャップをクローズしていくという。2011年9月7〜8日に米ボストンで開催された米シーメンスPLMソフトウェア主催のアナリスト・カンファレンスにおいて同社の最高技術責任者(CTO)であるChuck Grindstaff氏が語った言葉だ。
つまり、Grindstaff氏によるとシーメンスPLMソフトウェアでは、設計やマネジメントと、実際の生産拠点のオペレーションの間のギャップを埋めていくというのだ。
さまざまなITの投入の結果として、製品開発から生産への流れが完全にシリアルな順を追ったバトンリレーのような手順から、ある程度の双方向性を持ってきたことは間違いがないだろう。だが、現状の業務プロセスでもまだ不十分で、個々のプロセス間にはギャップが存在する、というのがGrindstaff氏の主張だ。
Grindstaff氏の指摘するギャップの1つは、PLMの設計・開発プロセス部分とMESなどを持つ生産プロセス側の間に存在する。ここでいう生産プロセスには、生産技術の検討部門や生産管理部門などの業務が含まれる。
具体的には、PLMシステムとMES(Manufacturing Execution System)をつなぐということだ。システムとしては、既に2007年に実現できているものだ(本稿末コラム参照)。
3次元CADなどで設計された「プロダクト(製品)」が、「プロダクション(製造)」していくシステムと統合されるということになる。つまり、製品企画から製品設計、生産準備、実際の生産工程から、サービス/サポートまでのプロセスが実際につながるという意味だ。
PLMシステムで管理された、E-BOMやM-BOMなどからは、さまざまな設計情報の他、ツールやリソースなどがMESに渡される。一方でプロセスチェンジなどの情報がMESからPLMに戻されれば、次のプロセスからは更新された情報がPLMからMESに渡る。
PLMシステムとMESが連携する利点は、例えば、ラインバランシングやリソースの最適化、互いの情報がシンクロされリアルタイムで更新されるために常に最新情報でお互いに仕事ができる、などのことがあるし、何よりもPLMやMES、さらにERPなどが完全に連携できることで、それまでに必要とされていたさまざまな冗長性を最小限にすることも可能になってくる。
これにより、いままではリアルタイムに連携できなかった領域の改善が見込めることになり、生産効率をさらに向上させることができるというのだ。以降で詳細を見ていこう。
保守プロセスの統合
まず、プロセス全体に関わってくるものとして挙げられているのが、「統合された保守管理」だ。
設計フェーズから、生産、保守フェーズに至るまでの製品構成情報を一貫して管理することは容易ではない。プロセスとBOMとが統合されていないからだ。BOMとBOP(Bill of Process)が統合されていれば、双方向で変更管理を行うことができる。同じデータを参照・更新していくのであれば情報の鮮度差によるミスも防ぐことができる。一貫したBOMができるため、設計からサポートまで1つの閉じたループの中で管理していくことが現実的になるのだ。
品質管理プロセスを考慮した設計
次に「統合された品質管理」環境の提供だ。計画段階で品質管理のためにどのようなインスペクション作業が必要なのか、その手順や指示書を作るのは簡単な作業ではない。
製品の情報と、テスト計画やインスペクション計画の管理を統合することで、イシューマネジメント(品質に関する不具合情報の管理)や変更管理をより効率的にできるようになる。
昨今、多くの製造系企業がグローバルに展開しつつある。生産部門のみならず設計・開発部門すら世界中に分散する状況下においては、チェックプロセスの標準化による品質水準の維持が絶対的に必要とされている。各フェーズが持つシステムの情報の整合性がとれていること、プロセス標準をシステムとして用意していることは、グローバル企業におけるPLMシステムの必須要件といってよいだろう。
作業指示の3次元化
企画・開発・設計・生産準備……メンテナンス・廃棄などの各フェーズが持つ情報が統合されればデジタルな作業計画も作りやすくなる。
例えば、PLMシステムで管理されている3次元CAD図面の情報を後工程で活用していくことで、組み付け指示やメンテナンスマニュアル作成といった、重複した作業を省略し、図面からダイレクトかつ分かりやすい作業指示を示すことも可能になる。
*** 一部省略されたコンテンツがあります。PC版でご覧ください。 ***
このように多様なメリットのありそうなPLMシステムと生産プロセスとの統合だが、当然そこまでの工程にはハードルもある。ここからは私なりの視点で考えてみたい。客観的に第三者として見た場合にポイントとなるのは、PLMシステム、MESをはじめとする生産システム双方がそれなりに稼働しているかどうかという点だ。
MESとPLM、適切なプロセスで運用されているか?
今回、Grindstaff氏がメリットとして強調していたのは、PLMとMESという2つのシステムが「統合」されることによって実現されるものである。つまり、まずはPLMシステム、MESシステムともに一定の水準で運用されていることが大前提となっている。
現段階では、多くの企業で製品開発を支援するPLMシステム、あるいは生産を支援していくMESシステムともに、個々の運用状況を見ても「究極の効率化」ができているか、という意味ではまだ改善の余地があるだろう。ここに「効率化し切れていないギャップ」があるのは間違いない。
だが、企業によっては、3次元CADやPLMシステムの導入がある程度進んでいて、なおかつ実際に生産を実行していくためのMESやMES同等のシステムの導入も進んでいるところもある。もし、そうであれば、個々のシステムの運用度を高めるだけでなく、「プロダクト」と「プロダクション」の連携を真剣に考えるべき価値がある。
完璧でないところであっても、「プロダクト」と「プロダクション」とが連携し、本当の意味で製品のライフサイクルの効率化を目指さなければいけないことには代わりはない。
従来は、CAD/PLMベンダーサイドから、生産と関連してPLMの話を聞くことは必ずしも多くはなかった。Grindstaff氏のプレゼンテーションは、生産側からもPLMシステムを認識するよい機会であった。
オールインワンで企画・設計〜製造実行システムまでを提供する強み
シーメンスPLMソフトウェアの母体であるシーメンス自身はPLC、SCADAシステムやそれらの管理ツール類を提供する部門を持っている。2010年12月にはシーメンスのPLC向けに統合環境「TIAポータル」を発表、PLCの制御や管理そのものの効率化を図っている(参考記事参照)。
シーメンスおよびシーメンスPLMソフトウェアでは、自社製品内でのMESとPLMの連携そのものを2007年の段階で実現している。
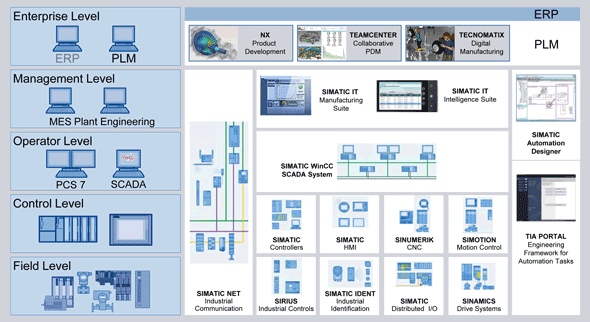
ERP以外の領域を全て提供できるのがシーメンスおよびシーメンスPLMソフトウェアの強みの1つ Grindstaff氏は「Top FloorからShop FloorまでのAutomationを図る」ことで、設計やマネジメントプロセス、実際の生産拠点のオペレーションの間のギャップを埋めていくことができるとする。注目すべきは図の左側だ。ここでは財務会計系の基幹システムであるERPとPLMは並列にエンタープライズシステムとして位置付けられている
3次元の仮想検証環境を利用しない場合のライン立ち上げでは、製品そのものの設計はもちろん、製造設備の設計が完了し、実機が出来上がった段階から検証が行われるのが一般的だ。設計フェーズも、設備設計も完了した後に何らかのミスが発覚した場合は大幅な手戻りが発生する場合もあり得る。前段階での手戻りは後工程を圧迫する。ライン立ち上げ準備の最終工程に位置付けられる制御プログラムのテストや検証期間が圧迫され、場合によっては稼働後に問題が発生することもあり、財務に影響を与えるような問題となることもある。
シーメンスPLMソフトウェアの持つ仮想シミュレーション製品(Tecnomatix)では、既に主要なFA制御機器との連携を実現している。製造実行プログラムを含んだ製造技術の検証を仮想環境下で行えるようになっている。
(文責:編集部)
Copyright © ITmedia, Inc. All Rights Reserved.