豊田自動織機の終わりなきデジタル変革、設備をIoTで最適化:製造業DX
製造業においてIoT活用への関心は高まっている。その中で、いち早くIoTデータを集約するIoT基盤構築を進め、さらにこれらで集約したデータを活用し現実世界にフィードバックする仕組みにより製造現場における生産性向上につなげた成果を生み出したのが、豊田自動織機である。
製造業でもIoT(モノのインターネット)活用を含めたDX(デジタルトランスフォーメーション)への関心が高まっているが、多くの企業では「具体的な成果を得ることが難しい」や「全体最適につながる基盤作りがうまくいかない」というような声も多く、順調に進んでいるとはいえない状況が生まれている。こうした中で、いち早くIoTデータを集約するIoT基盤作りを進め、さらにこれらで集約したデータを活用し現実世界にフィードバックする仕組みにより、製造現場における生産性向上につなげた成果を生み出したのが、豊田自動織機である。
豊田自動織機ではどういう考え方でこれらの取り組みを進めたのだろうか。同社のIoT基盤「Global Architecture for Ultimate Dynamic IoT(通称GAUDI)」の考え方と、その具体的成果である製造設備における品質向上への取り組みについて紹介する。
豊田自動織機独自のデータ活用基盤へ
豊田自動織機は、1926年の創立。自動織機の開発を祖業とし、トヨタ自動車の母体となった企業である。現在は、自動車や自動車向けのエンジン、カーエアコン用コンプレッサーなどを扱う自動車部門、フォークリフトやAGVなどを扱う産業車両部門、織機や紡機を扱う繊維機械部門の3部門で事業を展開している。特にフォークリフト、カーエアコン用コンプレッサー、エアジェット織機の3製品では、世界でも高いシェアを誇る。
これらの多様な事業展開を行う豊田自動織機だが、IoT活用に本格的に取り組み始めたのは2016年ごろだという。きっかけは情報システム部からの働きかけだった。
豊田自動織機 情報システム部 IT R&D推進室 デジタル技術グループ グループマネジャーの大橋健児氏は「2016年当時は、ドイツの『インダストリー4.0』や米国発の『インダストリアルインターネットコンソーシアム(IIC)』などの取り組みが世に示され、急速に関心が高まり始めたころでした。一方で情報システム部でも単に事業部門のニーズを受けて対応するだけでなく、提案型の組織となって会社の革新に貢献していきたいという思いがありました。そうした中で着目したのがIoTやAI(人工知能)などのテクノロジーでした。トヨタ生産方式(TPS)をはじめ、豊田自動織機には独自のノウハウや知見があります。これらを生かしたデータ活用の形を実現することが新しい付加価値につながると考えました。そこで、これらの基盤となる全社IoT標準基盤の着想を得て、開発を開始しました」と振り返る。
IoTでは、データを現場から取得して集めてきて蓄積し、そのデータを分析して知見を導き出して活用するというのが基本だ。さらに得られた知見を現実世界にフィードバックするというステップが一般的だが、豊田自動織機が開発する全社IoT標準基盤「GAUDI」もこれらに合わせて、機能を「とる」「ためる」「活用する」「フィードバックする」の4つに分解して開発を進めてきた。
この内「とる」「ためる」「活用する」の3つの機能から開発を進め、生産現場への実装を開始。複数の事業部と共同でPoC(実証実験)やシステム構築を行ってきた。例えば、作業者が装着したウェアラブル型のセンサーから生体情報(3軸加速度、心拍など)を取得し、生産性向上に役立てるといった取り組みもその1つだ。普段と異なる状況や不慣れな環境による“焦り”などによる作業遅れを検知するほか、生体情報と環境情報(温度、湿度)をひも付けて作業者の体調変化を検知し、熱中症を予防するなどさまざまな活動を行ってきた。
設備の最適パラメータを自動算出
さらにこれらをブラッシュアップし、2020年5月からは「フィードバックする」も含めた機能強化を行い、実用化に向けた取り組みを進めている。2020年8月から工場で運用を開始したのが、製造設備での品質向上への取り組みである。
製造設備では、設備そのものの製造用パラメータに加え、温度や湿度などの環境や素材などの投入材料の変化に大きく影響を受ける。そのため、変化する環境条件に合わせてパラメータを変更する必要がある。製造現場では熟練の作業員がその時々の状況に合わせてこのパラメータを設定し直しており、これによって不良品の発生を抑えている。「熟練作業員の知見や作業をシステム化する」ということに取り組んだのだ。
豊田自動織機 情報システム部 IT R&D推進室 デジタル技術グループ 1ワーキンググループ ワーキングリーダーの岡田具紀氏は「設備には既に数多くのセンサーが取り付けられており、データを取得できる仕組みが備えられていました。これらのセンサーから集めたデータをクラウドに蓄積しAIで学習させ、これをリアルタイムに分析することで異常を予知します。そして『このまま運転を続ければ不良品を作ってしまうおそれがある』と判断した場合、正常値に戻すための推論を進め、変更すべきパラメータの推奨値を自動的に算出するという仕組みです」とシステムの概要を説明する。
実際にこのシステムの運用により、製造現場において調整を行っていた熟練作業者の省力化につながったという。豊田自動織機 情報システム部 IT R&D推進室 デジタル技術グループ 1ワーキンググループの小浦祐輝氏は「これまで製造現場では作業者を配置して調整や不良の確認を行っていました。しかし、新たなシステムの活用により、不良品が出そうな場合の当たりがつけやすくなったなどの効果で品質確認工数の削減が可能になりました。また、パラメータ変更タイミングの推定やパラメータ推奨値の算出など、熟練作業者でなければできない作業も行えるようになりました」と語っている。
製造現場では人手不足が続いており、熟練作業者の負荷が高まっており将来的に「人がやるべき仕事」を選別していく必要性が生まれている。そこで、さらなるステップとして、「GAUDI」を直接連携させた自動制御も視野に入れているという。「現状では『GAUDI』でAIが算出したパラメータの推奨値をいったん作業者が受け取って確認し、問題ないと判断した上で設備に投入するという運用を取っています。こちらは製造現場と慎重に評価を進めていますが、このパラメータの提示内容の確認と並行し、『GAUDI』でAIが算出した新たなパラメータを設備に直接投入するという運用への切替作業も2021年3月末に完了しました。この切替作業についても、『GAUDI』のおかげで短期間での実施が可能になりました」と岡田氏は語っている。
この「GAUDI」をベースとしたシステムが優れている点は、こうしたアプリケーションをソフトウェアモジュールの組み合わせで実現しているという点である。これらの組み合わせにより、必要な機能を付加したり減らしたりしながら、同様の機能を他の環境でも容易に展開することが可能となる。「この故障予知のソリューションは特化したものではなく、データを取得できる機械であれば、適用することが可能です。データそのものを入れ替えることができれば、さまざまなところに水平展開できるように最初から構想して作り上げてきたことがシステムの特徴だといえます」と岡田氏は述べている。
「エッジ」「フォグ」「クラウド」の3階層アーキテクチャ
このような柔軟性のあるシステム構築はどのような考えで構築されているのだろうか。「GAUDI」のベースとなっているのは、マイクロソフトのクラウド基盤である「Microsoft Azure」および「Azure IoT Edge」「Azure Machine Learning」などのソリューションを活用して構築された「エッジ」「フォグ」「クラウド」の3階層からなるアーキテクチャである。
IoTシステムでは、現場に近いところでデータを収集したり、さまざまなロジックを実行したりする基盤と、現場から集めた膨大なデータを高速に処理する高性能な基盤を柔軟に連携させることが求められる。
これらに対応するため現場のデータの発生源に近い領域で情報を処理する「エッジ層」、クラウドで大容量データを処理する「クラウド層」、さらに両者を中継してデータを整流化する役目を担う「フォグ層」の3つの層を構築し、それぞれの要件を吸収するという考えとしている。「IoTを取り巻く環境を考えた場合、こうした3つの層での考え方が合理的だと考えました。マイクロソフトは2016年当時からエッジ、フォグ、クラウドの3階層をトータルでサポートしており、その中でのデータ連携やアプリケーション連携などのツールも豊富に用意していたことから、われわれは一貫してMicrosoft Azureを活用してきました」と大橋氏は語っている。
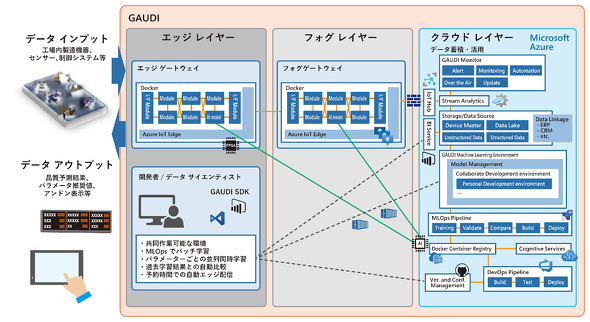
豊田自動織機の全社標準IoT基盤「GAUDI」の全体像。マイクロソフト テクノロジーを活用し、エッジ、フォグ、クラウドのいずれでも同じソフトウェアモジュールを稼働可能。これにより幅広いユースケースへの適用を迅速かつ低コストに実現できる(クリックで拡大)出典:豊田自動織機
この3階層のアーキテクチャの利点として、GAUDIの構築を担当する豊田自動織機 ITソリューションズ DXビジネス推進部 DXシステム開発課 1グループ グループリーダーの兵頭亮哉氏は「最大のメリットは、開発したロジックを必要に応じて素早く展開できることです。Microsoft Azureが提供するコンテナ技術を使ってマイクロサービス化することで、クラウド、フォグ、エッジのどこでも場所を問わずにそのまま動かすことができます。豊田自動織機は事業領域が多岐にわたるため、より細かく、明確にマイクロサービス化を行うことで流用率を向上させる工夫をしています。また、固有処理(カスタムロジック)が必要になると想定しているため、カスタムロジックについても共通ロジックと同様に扱えるように工夫をしています。これらに加え、DevOps/MLOpsを適切に運用することで開発の効率を上げるだけでなく、ユーザーの運用にも適用し作業効率の改善を行っています」と語る。
先述した設備のパラメータ設定を最適化するシステムを例にとって考えてみよう。設備に設置された多数のセンサーから収集した膨大な稼働データを蓄積し、機械学習を行って最適なパラメータを算出するためには大量のコンピューティングリソースを必要とする。そのため、この作業には「クラウド層」のMicrosoft Azure上の仮想マシンやストレージ、データベースを利用することが合理的だといえる。「クラウド層」で作成された推論モデルだが、実際に運用するにはリアルタイムで品質情報などを伝える必要があり、「クラウド層」ではタイムラグが問題になる。そこでこの推論モデルを現場に近い「エッジ層」に展開することが必要になる。
このように用途に応じた柔軟な変更に対応できるのである。これにより、開発の負荷低減や効率的な運用の両立を実現できる。また、同じ推論モデルを、工場をまたいで複数の製造機械に展開したり入れ替えたりすることも容易となるわけである。
工場DXに向け「線」から「面」へ拡大
豊田自動織機では、「GAUDI」の今後も継続的な機能強化を図りつつ適用領域を拡大していく方針だ。「そもそもGAUDIという名称は、アントニオ・ガウディのサグラダ・ファミリアになぞらえ、終わりなく常に新しい機能を実装し続けていくという意味が込められています。IoTやDXによる企業変革も終わりのないものですので、これらの動きに対応できるように進化させていくことが重要だと考えています。また、1つの装置だけに閉じて生産性向上を図ることもIoTの使いどころではありますが、その前後工程からライン全体、工場全体をつなぎ、さらにはサプライチェーン全体をつないだデータ活用を実現してこそ、はじめてIoT本来の価値を創出できると考えています。製造現場と足並みをそろえながら、GAUDIの適用領域を点から線、面へ広げていきたい」と大橋氏は語っている。
製造現場の期待も高まっており、ある工場では設備の稼働情報や品質情報などあらゆるデータをGAUDIに集めて可視化や分析をすることで、工場のスマート化を実現する動きも実際に進んでいる。また、一方で製品のIoT化に対する基盤として「GAUDI」を活用する取り組みも進んでいる。フォークリフトなどの主要製品にIoTの仕組みを組み込み、顧客に対して稼働状況の遠隔監視や予防保守などのマネージドサービスを提供する基盤として活用する構想だ。
現時点ではGAUDIの新たな機能実装はITの専門知識をもった開発者でなければ困難だが、将来的には製造現場のユーザーが自分たちだけでも必要なIoTを実現できる環境を提供する考えだ。岡田氏は「誰でも使えるようにする『IoTの民主化』のような形が理想です」と考えを述べる。例えば、「IoT環境の構築や変更の自動化(オートメーション機能)」「ほしいデータがすぐに取得可能なデバイス」「GUIによるデータベースアクセスをサポート」「GUIによる機能設定やAIモデルの配信」「データ分析でよく使う機能やテクニックの提供」「モノづくりのノウハウを織り込んだ豊田自動織機独自のデータベース設計」といった機能やサービスを実現することを目指しているという。
IoTやデジタル変革などへの取り組みは「終わりのない旅(ジャーニー)」に例えられることも多い。アントニオ・ガウディの代表作であるサグラダ・ファミリアはデジタル技術により後300年かかるとされていた完成時期が2026年に早まったとされるが、同じ「GAUDI」の名を冠する豊田自動織機のIoTへの旅は、まだ始まったばかりだ。
Copyright © ITmedia, Inc. All Rights Reserved.
関連記事
- デジタルで“品質”を再定義、細分化し複雑化する製品開発に対応せよ
- “想定外”に対応する「レジリエント・サプライチェーン」をどう実現するか
- COVID-19で製造業はどう変わる? 高まる「復元力」「機動力」の優先度
- デジタルツインで加速する設計環境のデジタル変革、何ができるようになるのか
- マイクロソフトの製造業担当トップが強調する、DX4つの論点とその前提にあるもの
関連リンク
提供:日本マイクロソフト株式会社
アイティメディア営業企画/制作:MONOist 編集部/掲載内容有効期限:2021年5月15日